Reliant Machinery Ltd.
Address
Reliant Machinery Ltd.
Unit L Cradock Road
Luton
LU4 0JF
Grossbritannien und Nordirland
Telephone+44 1582 584999
Fax+44 1582 581117
Discover more from us
Follow us on
About us
Reliant Machinery Ltd. is the world's leading manufacturer of innovative flatbed laminating, fusing, heat transfer, powder coater, and converting equipment. Indeed, Reliant is the original patent holder of this technology and has produced dual belt flatbed laminators for over 50 years.
The continuous development of new materials for countless applications sets endless challenges to processing technology. Therefore, adhesive bonding and flatbed laminators are the foundation of modern industry because this combination allows the assembly of multi-strata of the same or different substrates, creating ground-breaking lightweight multi-material structures.
Today, dry-heat adhesive lamination is the backbone of ultra-competitive industries like automotive, composites, aerospace, insulation, defence, medical, filtration, and many others.
Only to mention a few advantages of Reliant laminating technologies, we can point out:
Uniform and constant pressure and the highest thermal efficiency
- No thermal distortion, stress or changes in the structure of the substrates
- Flexibility and versatility – It is possible to laminate all sorts of substrates
- VOCs, solvents, toxins and fumes free
- Evenly distributed stresses over the entire bonding area
- Excellent fatigue strength/resistance of adhesively bonded joints
- Substantial reduction of weight without compromising the bonding strength
- Possibility to create materials that are light and strong
- No losses – one metre of adhesive equals one metre of laminated material
- No damages caused by mechanical fasteners – needles, rivets or screws
- Lean Manufacturing – fewer process steps and less workforce
Reliant production range comprises the following equipment:
- Flatbed, dual belt laminators from 0.45 to 3.0 metres wide
- Laminators with or without internal cooling
- Laminators with or without tunnel height adjustment
- Powder coaters
- Infrared hood
- Cross-cutters, guillotine cutters, and sheeters
- Slitting systems and edge trimmers
- High-sensitive tension control winders
- Stacker units
- Pick and place stations
- Accumulators
And
- Complete range of fusing machines for the best and top-quality garments
Reliant's straight-thru design has been a staple in the laminating and consolidation markets. The modular designed system of heating, cooling, and pressure allows the capacity of each machine to fit the process parameters required by our customers.
The whole line of Reliant laminators can process woven fabrics (rigid or elastic), knitted fabric, warp knits, nonwoven, unidirectional, multiaxial, spacer fabric, leather, artificial leather, foams (PU, silicone, etc.), metals, wood, plywood, and many others. From a fraction of a millimetre up to 150mm thick material, we always have the best possible solution.
Today, Reliant Powerbond's range of laminators is the leading machine worldwide in a wide variety of sectors. It all started about 25 years ago with the launch of the SPL model; then, based on the inputs of our customers and the needs of the new materials and polymers, we developed the HPL and HPC models.
Powerbond SPL – Standard Pressure Lamination
Powerbond HPL – High-Pressure Lamination
Powerbond HPC – High-Pressure Compression
The Powerbond range is suitable for processing light and delicate formats, sensitive fibres or the heaviest substrate, and flexible, semi-rigid and rigid materials.
All three models have in common the following features:
- Modular construction – with extendable heating and cooling sections
- Single or multiple sets of pressure rollers
- Driven tunnel gap adjustment from 0 to 150mm in 0.1mm steps
- Independent nip roller gap adjustment
- Pre-joined or endless, mark-free processing belts
- Easy and fast belt-changing system
- Perfect and accurate processing belts tracking and tensioning
- Wide range of power options
- Multiple and individual heating zones control
- PLC/HMI with self-diagnosis and complete control of the process
Reliant's laminators stand out in their performance while using dry-heat adhesives in web, film, and powder formats made of any polymer and PSA. Once again, guided by the market, we paid particular attention to our powder scattering units.
Reliant has been manufacturing powder coaters for over 30 years and, during this time, developed, perfected and patented some scattering technologies. From a few grams, as low as 5 g/m² of powder adhesive or epoxy resin, to a much heavier load of PLA for bio-composites, our Powerline powder coaters scatter the polymers across the substrates with high accuracy and perfect uniformity.
The main features of our Powerline powder coaters are:
- Widths from 0.6 to 3.0 metres
- High-volume powder reservoir
- Adjustable sliding dam plates for powder width control
- Levelling system to ensure even distribution of powder inside the hopper (depending on the width)
- Low powder level warning sensor
- High-accuracy adjustable doctor blade
- Variable-speed powder pickup roller
- Variety of pickup rollers for a wide range of particle sizes
- PTFE mesh conveyor belt
- Conveyor cleaning system
- Powder collection hopper for recycling
- Manual or automatic hopper height adjustment
- An anti-static bar for even powder dispensing
- PLC control of powder volume and speed
- As an option, automatic feeding systems
Reliant's Powerline powder coaters can be part of a new line or retrofitted into any existing coating line. Furthermore, we can install multiple scattering units on the same line and on wheels and rails to modify the production configuration.
All laminators manufactured by Reliant can work stand-alone or as a complete line; to do so, we offer a wide range of bespoke handling equipment, including unwinders, rewinders, accumulators, nip systems, and others. Reliant's range of winders covers the most delicate tension-sensitive substrate to the heaviest material.
The Rolamatic range is suitable for lightweight rolls of materials, while the Powerline is our heavy-duty range suited for heavy rolls. The main features of both are:
- From a few kilos to 4.000 kg capacity per position
- Driven and non-driven units
- Centre, surface and cantilevered models
- Single or multi-positions
- Wide selection of shafts, core chucks, and safety chucks
- Low, middle and high-level positioning
- Manual or automatic edge guide
- Fixed on the floor or mounted on rails with quick-release connections
The laminating process in Reliant's machines is tension-free; therefore, you can laminate, among other materials, bi-elastic warp knits or multiaxial hybrid fabrics without any distortion. However, the handling equipment is also crucial for tension-free processes; poor tension control leads to many material faults and poor roll formation, wrinkles, web stretching, roll blocking, crushed cores, telescopic rolls, and many other problems.
For that reason, we developed several tension control systems for unwinders and rewinders as follows:
- Pneumatic brake and manual settings
- Pneumatic brake and diameter sensor with HMI settings
- Magnetic particle brake and manual settings
- Magnetic particle brake and diameter sensor with HMI settings
- Load cells with HMI settings – Pneumatic brake tension
- Load cells with HMI settings – Magnetic particle brake tension
- Load cells with HMI settings – Motor driven
- Dancer roller – Motor driven
- Dancer roller + loop sensor - Motor driven for low tension
- Hybrid systems
Also, to complement our laminating lines, we manufacture cross-cutters, slitters and edge trimmers for smooth operations and easy roll replacement in our rewinding units. Besides, for continuous and non-stop processing, we have a line of accumulators for pre or post-lamination.
To make our customers' lives easier, we have testing facilities in Luton (about 50 km North of London), Philadelphia and North Carolina in the USA.
If you have any project which requires a laminator, a powder coater, or handling or converting equipment, get in touch, and we will gladly assist you.
Our product groups
- Technology and Processes
- Bondtec (Surface & Bonding Techniques)
Our application areas / Solutions
Keywords
- Compression Machines
- Fusing Equipment
- Coating Machines
- Bonding Equipment
- Laminating Machines
Our Products
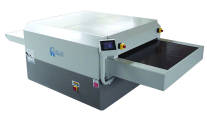
Fusing Machines
Benefits of Reliant’s Fusing Machines
The elimination of fabric shrinkage, bubbling and other distortions, and heat shock effects on the fabric
The elimination of “Strike back” and “Strikethrough” of adhesive onto fabric surfaces and machinery
Flexibility of production including complete range of modern fabrics such as micro-fibers, viscose and viscose mixtures, lycra mixtures, etc. as well as the full range of interlinings
The elimination of expensive re-cuts and returned garments
Cost savings resulting from all of these technology benefits
Reliant offers, basically, four models of Fusing presses: Coolstream, Excel, Elite and Nova 45.
Coolstream High Production Fusing Press
The Coolstream is the state of the art fusing press for high volume production where quality control and finish is paramount. The Coolstream Fusing Press brings the best in fusing technology to the volume production factory.
The Coolstream fusing press is designed for the high quality production of all types of fused garment parts. It is especially effective for high quality outerwear fabrics where high volume throughput while maintaining the highest quality standards is required. It is for these reasons that some of the largest and best-known men’s suit manufacturers around the world use the Coolstream machine for their production.
Excel II Fusing Machine
The Excel II model brought 21st century PLC control technology to the well-tried and tested Reliant Excel range.
This machine offers superb quality fusing output for all types of fusing production from heavy weight outerwear, shirt collars and components right through to lightweight blouses, dresses and casual wear.
Elite M60 & M90 Fusing Machine
The Elite Fusing Machine Range brings the output quality of larger fusing equipment to a compact system.
The Elite offers great quality standards at a very affordable cost and space requirement and is suitable for all types of fusing output up to 90cm widths.
Nova 45 PN Fusing Machine
The Nova brings high pressure fusing to a small compact machine which can be used as a stand alone or in-line production system.
Noanother machine of this size and class offers fully adjustable pneumatic pressure which guarantees the output quality for all types of small parts, waistbands, etc.
- PLC programmable controls with built in job memory
- Low temperature fusing
- Horizontal flat run tunnel
- Elimination of shrinkage & fabric distortion
- Power consumption – heat saving
- Tri zone heating and control via PLC
- PID temperature control via PLC
- Auto compensating “floater heater” modules
- Conveyor Belt Sensing Zone (BSZ)
- Synchro-Trak belt tracking
- High pressure capability
- Effective fabric cooling
- Automatic four stage cleaning
- Controls and self diagnostics via PLC
- Pneumatic high pressure capability for high quality output
- Guaranteed even pressure for consistent quality production
- Heating layout ensures even temperatures
- Accurate temperature control for better quality output
- Straight through tunnel layout ensures no distortions
- Ergonomic design for efficient production
- Easy maintenance system ensures high reliability
- Wide width fusing capabilities for all fabric sizes
- Flexible production system
- Easy to view controls
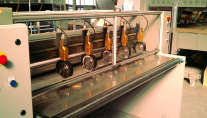
Coverting Equipment
Reliant Cutting and Peripheral Handling Equipment
Reliant Machinery Ltd, in conjunction with its associate companies, produces a wide range of equipment for in-line processing of all types of materials. This allows the company to provide a complete turnkey solution for customers who need to carry out downstream processing of their materials after lamination.
The range includes, in line cutting in the X & Y axis of both soft, flexible and rigid materials. Cutting can be carried out on moving webs as they exit the laminator by travelling or stop-start systems, depending on the materials. Incorporated in the range available is edge trimming and slitting with cut waste handling, accurate cross cutting on the moving web to allow sheets and short rolls to be continuously produced from web fed materials, multi-lane narrow width tape slitting, integrated twin turret rewinding for in line changeovers, tube cutters.
In addition to the cutting equipment, Reliant also produces accumulators and splicing systems for continuous production, automatic de-stacking and re-stacking systems for automated sheet feeding and offloading, corner trimming, edge folding and back wrapping for panel production, in-line ultra-sonic systems. Reliant will also consider the design and production of in-line custom built systems to enable customers to process products requiring specialized handling.
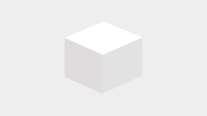
Laminating Machines
The Powerbond range is divided in HPC, HPL and SPL models; it is Reliant’s flagship laminator range, incorporating the unique, well-tried and tested modular construction.
The Powerbond range is used in many different industries for materials starting with films of a few microns thick, through to products of up to 150mm thick.The design allows machines to be assembled to fit exactly to the customer’s production specifications.
The Powerbond-HPC brings Reliant’s fully modular assembly together with a high-pressure system capable of applying significantly increased levels of pressure during heating and cooling.
The Powerbond HPL, due to Its robust design is ideal for products requiring significant pressure and contact during the lamination. But don’t need to be fully compacted during the process.
The design of our Powerbond SPL starts with a 1700mm heating section, additional 1000mm sections of heating, cooling and pressure systems, can be assembled together to provide a machine of any capacity required.
The Coolstream TAL provides high volume laminating capacity with the flexibility to bond thicker products, using its height adjustbale lamination tunnel. Products up to 50mm thick can be laminated on this machine making it highly adaptable and suitable for processing a wide range of materials including foams, composites, nonwovens, breathable membranes, textiles and others.
The Coolstream MPG range provides a medium to the high capacity laminating system at an affordable cost. The unique Reliant GOS (Gap Opening System) allows both thin and resilient materials to be processed through the machine without adding significant cost to the equipment.
The Magnum GOS range brings reliable, high quality, performance equipment, into a lower dimension of investment for smaller and medium processing volume requirements. The Magnum incorporates features normally only available on larger and costly machines. These include the ability to laminate multy-layer laminates in one pass, feeding of sheets, reel-to-reel or sheet-reel-sheet formats.
The Compact HCL is a cost-effective way to create laminates with both heating and cooling sections. The Compact HCL combines many functions and advantages of Reliant’s larger equipment, like zoned PID controlled heating and pneumatic pressure on a much smaller scale. Using the mechanical adjustment, the tunnel will allow thicker materials to be processed by manually setting the gap between the belts to a maximum of 25mm.