VB-SET S.r.l.
Address
VB-SET S.r.l.
Via Tevere 1
20020 Vanzaghello Milano
Italy
Telephone+39 0331 307143
Fax+39 0331 307999
Discover more from us
Follow us on
About us
VB-SET is an Italian company specialised in innovative extrusion spinning machines for the production of continuous filament synthetic yarn. We have more than 20 years of experience in this field, with background of more than 500 spinning machines installed worldwide for POY, FDY, IDY (Technical yarn), dope dyed (solution dyed), Bicomponent, Monofilament, Laboratory machines, Pilot machines.
All designs and process know-how are VB-SET property. Machine manufacturing is made in VB SET workshops.
VB SET is focused to create value for his Customers:
- Each spinning machine has technical features for the maximum of flexibility to allow the production of wide variety of products.
- Each spinning concept is designed for a pre-assembling in our workshop to allow easy and fast erection at the Customer site.
- All machines have full electronic control with all process parameters continuously monitored according to the most modern standards
- Our flexible design approach allows to customise our machines to respond to our Customer needs
- Our technical team is engaged in new machine design challenge to produce speciality yarns and to process new polymers.
- VB SET is Customer oriented, ready to cooperate in order to design for them “exclusive” machines, according to Customer or joint developed process know-how
VB SET is located very closed to the Milan Malpensa airport, to make very easy for our Customers to visit us anytime to discuss their needs and requests.
VB SET supplies complete spinning machines and, upon request, components for spinning machines, like extruders, polymer melt distribution system, spinning head, quench cabinets, draw field.
For the production of polyester and polyamide (nylon) Industrial yarn VB SET supplies EASYSPIN ONE, a multi module spin draw machine based on a very innovative draw field set up
Special focus is on the single-double module spinning machines for polyester, polyamide and polypropylene. For this purpose, VB-SET has developed “EASYSPIN FLEX”, small and flexible, that can run different polymers with different machine set-up, suitable to produce yarn for textile and Industrial application.
All spinning machines can be provided with VB-MAST, a dope dyed injection and mixing system that allows to achieve best colour uniformity.
VB-MONO is the new monofilament product line for polyester, polyamide, polypropylene and HDPE, designed for the most critical monofilament application
EASYSPIN-LAB is the compact, flexible laboratory and/or pilot machine developed for testing and developing raw material and yarn.
On the field of production of polyester and polyamide yarns for textile application, VB-SET supplies a full range of parallel spinning machines to satisfy all Customer needs. Machine design for textile yarn production have a very flexible design in order to produce POY, HOY & FDY.
VB-SET can provide as well full engineering services:
- Basic engineering
- Detailed engineering
- Specification of ancillary equipment
- Process control system
- New process developmenent according to Customer needs
- Software design for machine supervision
- Software design for machine productivity management
- Utilities engineering
Our product groups
- Technology and Processes
Our application areas / Solutions
Keywords
- laboratory
- pilot
- tenacity
- spinning
- monofilament
Our Products
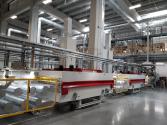
VB - MONO spinning systems for monofilament production
VB-MONO concept is an extrusion line designed to produce high quality monofilament yarns processing standard polymers like PET, PA6, PA66, PBT, PP, PE.
The line can be designed with technological upgrade in order to process high performance polymers like PA12, PLA, PPS, etc.
Each line is designed for an optimum diameter range depending from number of monofilament and required throughput
Highlights:
- Produce diameter ranges from 0,07 to 2,00 mm.
- Process standard polymers and high performance polymers
- Available design for production of bicomponent monofilament
- Draw of the monofilament in hot air oven, steam or water bath
- Annealing of the monofilament in hot air ovens
- Low energy cost
- Easy maintenance
High quality monofilament
All components are designed to keep high precision on temperature uniformity in extrusion, polymer distribution, spinneret heating, filament cooling, godets, stretching and annealing ovens. The result is a uniform product with low CV of the main product parameters.
Spinning performance
Polymer melt distribution in the spin pack/spinneret and the choice of mixing points of the melt stream allows narrow deviation of the filament size and even monofilament section.
Low residence time respecting the ideal melt polymer share rate allow minimum degradation of the polymer, to reach yarn tenacity level up to 7 gpd.
Stretching and annealing
Air ovens are designed to keep temperature variation within 1 degree from set point. The airflow is laminar, and the monofilaments inside the oven maintain straight path with minimum vibration
Different machine set-up for all kind of monofilament yarn
Monofilament machine can be supplied with one extruder or with two extruders for bi-colour of bicomponent yarn production.
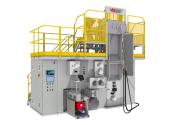
EASYSPIN LAB: Modern high quality Compact Laboratory - Pilot spinning machine
Testing of polymer and additives for yarn production
EASYSPIN-LAB concept is the compact Laboratory and Pilot spinning machine especially suitable for:
- Colour matching
- Testing of spinnability of polymer and chemical materials
- Production of material samples
- Development of new fibres for special applications
- Production of small lots of fibres
- Research on polymers and fibres
We provide:
- Solutions for different spinning processes POY, FDY, HT, BCF with the possibility to run some or all of these processes on the same machine.
- Solutions for producing yarn homo-polymer and bicomponent
- Design for processing all standard polymers (PET, co-PET, PA, PP, PBT, PTT, PLA etc)
- Design for processing high performance polymer (PEEK, PVDF, ECTFE, ETFE, FEP, PFA, etc)
- Design for processing resorbable polymers for medical sector
- A variety of optional and customized solutions.
Models available:
- EASYSPIN-LAB1: suitable for POY
- EASYSPIN-LAB2: suitable for POY, FDY
- EASYSPIN-LAB3: suitable for POY, FDY, BCF
- EASYSPIN-LAB4: suitable for POY, FDY, HT
- EASYSPIN-LAB5: suitable for POY, FDY, HT, BCF
- EASYSPIN-LAB6: suitable for FDY, BCF Tri-color
All EASYSPIN-LAB equipment is available in the variant BICO, for bicomponent yarn
It is the ideal machine to test if a polymer is suitable for extrusion spinning and support its development
Flexible in processing yarn samples and small lots of yarn
The machine is available in several configuration depending from the yarn (type and denier range) to be produced. Machine can produce high speed yarn as POY, FDY, BSY, BCF, Technical Yarn.
Machine can be designed to run single polymer or bicomponent yarn
Flexible for colour matching
Design with short residence time allows a very quick colour change, ideal for efficient colour matching and colour development
Efficient research and development
Machine flexibility and easy operation allows yarn manufacturer, polymer and additive producers as well as research institutes to get a fast feedback from the yarn process for a efficient work on the research and development of new products
Compact Design
With its compact design the machine can be be installed inside small laboratory room. Machine is designed on plug & play philosophy and completely pre-tested in our workshop for easy installation on a laboratory.
Easy handing
Compact concept allows the lab machine to be operated by one operator only.
Custom made release
The machine concept allows further flexibility for Custom made realization, according to specific need in terms of polymer, denier range, dpf range, process temperature, process speeds.
VB MAST: dope dyed extrusion technology
VB-MAST side-extruder concept is the state-of the art solution to produce high quality dopedyed (solution dyed) yarn.
Dope dyed yarn spinning is year after year becoming a key factor to reduce the environmental impact of the package dyed and piece dyed processes. Producing colour yarn with VB-MAST technology eliminates all water pollution and discharge of harmful waste.
Highlights:
- VB-MAST is based on a dedicated design of dynamic mixer developed to allow a very uniform mixing of the white melt streamwith the coloured melt, without colour degradation.
- Accurate process control on pressure, temperature and mixer revolution speed allows to repeat the colour time after time. It is possible to adjust shade deviations inducted by variation in the raw material.
- Using dedicated side extruder to melt the master batch, the main extruder is never polluted.
- Melt injection unit is easy dismountable for fast cleaning.
- The colour melt dosing is performed by a metering pump for the most effective and precise dosing.
Wide experience
Since 1996 we successfully supply equipment for dope dyed spinning for POY, FDY, HOY, IDY. Our wide experience is at disposal of our Customer to enter in and develop this speciality business.
Colour uniformity
A dedicated design of dynamic mixer is developed to allow a very uniform mixing of the white melt stream with the coloured melt. The dynamic mixer can be installed as prolong of the main extruder screw or inserted in the polymer line.
Colour repeatability
Accurate process control on pressure, temperature and mixer revolution speed allows to repeat the colour time after time. It is possible to correct shade deviations inducted by variation in the raw material.
Fast colour change
Using dedicated side extruder to melt the master batch, the main extruder is never polluted. Melt injection unit is easy dismountable for fast cleaning. Mixing grooves in the dynamic mixer are shaped to avoid colour degradation.
Precision dosing
Using dedicated side extruder to melt the master batch, the colour melt dosing is performed by a metering pump for the most effective and precise dosing. In case of master batch dosing using a gravimetric unit system special installation of dosing unit are advised to minimize dosing errors due to vibrations.
Less degradation on master batch material
Parallel spinning design allows a complete pre-assembling and testing of all parts in our factory before shipment to assure a machine working faultless within few weeks from the delivery.
PET and PA spinning systems based on parallel spinning concept
EASYSPIN-FLEX concept is designed to be flexible in producing yarn from different polymers to cover a wide range of products for textile and technical application.
Compact design and fast change of product types and colours allows the production of small lots without compromising quality.
EASYSPIN-FLEX can produce POY-FDY-HT. Flexible design allows to produce each type of yarn in the same machine.
EASYSPIN-FLEX is based on a modular design that easily allows change machine configuration in order to produce different kind of yarn using an optimized yarn path.
EASYSPIN-FLEX is completely pre-assembled in our workshop before delivery to our Customer
Available in different configuration:
- Single module type 4/6/8/10/12
- Double module type 4+4/6+6/8+8/10+10/12+12
Highlights:
- Suitable for wide range of denier
- Design available for 4, 6, 8, 10, 12, 4+4, 6+6, 8+8, 10+10, 12+12 ends
- Suitable for different polymers: PET, PA, PP, PBT, PTT, etc.
- Suitable for POY-FDY-HT
- Dope dyed yarn with VB-MAST technology or traditional gravimetric system
- Any type of filament cross section: round, trilobal, hollow fibre, etc.
- Low energy cost
- Low cost easy maintenance
- Fast installation
Optimized yarn path
Linear compact design
Production flexibility
Easy string up
Easy and fast assembling on site
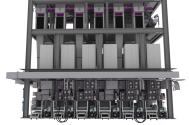
EasySpin One: Spin-draw Industrial (technical) yarn spinning machine
EASYSPIN-ONE, concept to produce high tenacity yarn for technical application, is based on our property design of Integrated Production Units (IPU):
- Each IPU is a spinning machine module available in different configurations, from Class1 to Class4, depending from the required range of denier.
- Number of IPU on each machine is defined according to the required capacity. Innovative IPU arrangement maintains a very short melt polymer residence time.
- IPU design minimizes contact points of yarn on thread-guides allowing higher production speed, less breaks and low broken filaments level.
- IPU compact draw field, where all components are easy to be managed by just one operator, allows an easy string-up.
- IPU lean design optimizes production cost
- The machine design allows a complete pre-assembling and testing of all parts in our factory before shipment to assure a very fast reassembling on site.
Highlights:
- Range of denier from 15 to 3000 Den
- Class 1, Class 2 and Class 4 arrangements
- Modular IPU design for:
- Tenacity above 9 gr/den
- Very low shrinkage yarn
- High quality yarn standard
- One operator only for draw field string up
- Low energy cost
- Low cost easy maintenance
- Fast installation
IPU – Integrated Production Unit
Concept is based on the design of highly integrated production units (IPU).
Each IPU is a spinning machine Class 1 for coarse denier, (1 end up to 3000 Den is processed in each draw field), Class 2 for medium denier (2 ends from 500 up to 1500 Denier is processed in each draw field), Class 4 for fine-medium denier (4 ends from 30 to 500 Denier is processed in each draw field)
Very short residence time
According to required capacity EasySpin One concept can combine the IPU by different arrangements, maintaining a very short melt polymer residence time.
Designed for high performance yarn
Equipment arrangement allows production of high performance yarn such high tenacity with very low shrinkage.
Optimized yarn path
IPU concept minimizes contact points of yarn on thread-guides allowing higher production speed, less yarn breaks and low broken filaments (fluffs) per bobbin
High full bobbin ratio
IPU concepts achieves the highest percentage of full bobbin ratio
Easy string up
IPU has a very compact draw field, where all components are easy to be managed by a single operator
Reduced maintenance cost
The most critical components are reduced in size with a innovative simplified design that allows fast, easy and inexpensive maintenance
Easy and fast assembling on site
IPU concepts allows a complete pre-assembling and testing of all parts in our factory before shipment to assure a machine working faultless within 4 weeks from the delivery.