Kansan Makina Kagit San Ve Tic A.S.
Address
Kansan Makina Kagit San Ve Tic A.S.
Capak Mahallesi No: 6
35860 Izmir
Türkiye
Discover more from us
About us
WETLAID LINE SOLUTIONS FROM KANSAN
Kansan Materials was established to supply complete wetlaid nonwoven lines and web forming technologies for the manufacturing of fully dispersible, biodegradable and environmentally friendly, sustainable materials for wet wipes, hygiene, filtration, healthcare, automotive, construction, and insulation industries to answer the increasing demand for sustainable raw materials.
Kansan Materials’ wetlaid production line consists of a headbox unit, hydroentanglement unit, a dewatering system, an air-thru dryer and a slitter winder, developed, designed, engineered and manufactured by Kansan.
Kansan Materials is a Kansan Group company, the leading machine manufacturer of fully automated and integrated wet wipe lines.
The wetlaid is a process where short fibers are suspended in a fluid, the fibers are deposited onto a screen or porous surface to remove the fluid, and the web is then consolidated mechanically, chemically, or thermally.
A wide range of natural and unnatural fibers can be used in the wetlaid process such as cotton, wool, hemp, jute, coconut, viscose fibers, fibers from PET, PP, aramid, carbon, glass, wood, ceramics and metal. The wetlaid technology allows the use of a combination of various fibers at the same time.
Kansan Materials provides energy-saving high-efficiency systems for you. The heat recovery system and facility heating are some of the engineering marvels of the Kansan R&D team.
- Heat Recovery System
To dry the web in the Air-Thru Dryer, clean air at ambient temperature is heated up to 180°C by burning natural gas. The heated air is then expelled as flue gas at the exhaust after the recirculation in the machine. If the temperature of clean air at the inlet of the machine can be increased then the natural gas energy consumed will decrease.
The flue gas can be mixed with clean air before the inlet at the heat exchanger. The clean air can be heated up to 60-70°C before entering the dryer. This way a significant amount of heat energy is recovered.
- Facility Heating
The facility heating and air conditioning work similarly as explained in the heat recovery system. The heated air coming out of the dryer can heat the main water of the facility with the help of a heat exchanger by extending the installation path.
It can also be used to heat the facility environment bypassing certain paths throughout the facility. By heating the mains water, energy saving can be achieved for the hot water to be used in the facility’s toilets and kitchens.
For more information about the nonwoven technologies of Kansan Materials visit kansanmak.com or contact us at info@kansanmaterials.com
Our product groups
- Technology and Processes
- Nonwovens
Our application areas / Solutions
Downloads
Keywords
- Wetlaid
- Web Forming
- Nonwoven Machines
- Headbox
- Hydroentanglement
Our Products
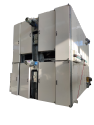
KM Dryer
Drying is an indispensable process where hydroentanglement is used for mechanical bonding. The web after Kansan Materials HydroJet, even it is dewatered with superior suction, is still fairly damp and needs to be dried out for further processing.
Kansan Materials high capacity Through-Air Dryer are installed in wet forming lines thanks to their high evaporation capacity. It’s suitable for evaporation from 30-80 gsm nonwovens composed of 20% lyocell 80% pulp.
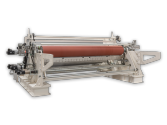
KM S-Winder
Slitter winder is the latest step of the nonwoven production process. The web that comes out of the line is winded over a cardboard or metal shaft. When the desired diameter is reached then the shaft is removed from the process and the new shaft is placed on the winder area. This change-over takes place non-stop at the line’s maximum running speed.
KM-SWinder is also equipped with longitudinal slitting blades that allow the slitting of full web width into narrower webs. The process is fully servo-driven and makes sure the finished rolls have the same tension and tightness throughout the winding process.
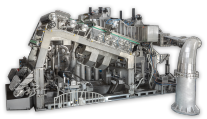
KM AquaFormer
KM-Aquaformer is the most crucial component of a wetlaid production line. It performs the entire wet laying steps. Wet laying is a mature and the most effective method that has been used in paper and wetlaid nonwoven industries for quite some time. This method allows the production of nonwoven materials from renewable and cost-effective, eco-friendly fibers like cellulose and pulp.
Wet former’s process flow is as follows:
- Water with fibers in suspension from the white water tank is pumped to the headbox.
- Fibers are laid on the mesh belt under the headbox. An inclined headbox design is used for fiber distribution and spacing to be homogenous and consecutive. The dilution ratio of fibers in water is very critical and needs to be adjusted optimally. The ratio changes based on the fiber type and fiber lengths.
- The pumping and flow pressure must be stable to ensure a constant flow of fibers on the mesh belt. The water gets through the mesh and is sucked while the fibers stay atop and form the web.
- The main goal is to have a very uniform web formation with desired porosity through a perfect fiber distribution where each fiber lands right next to the other without so much overlapping or hindrance.
- The excess water then is being recycled back to the white water tank for cost and energy saving.
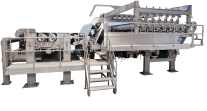
KM HydroJet
Hydroentanglement is a very fast and effective web bonding technology and the next process for wet lacing and spunlace. High-pressure water jets are used. The water is sprayed through the web on the mesh belts for fibers to entangle mechanically. The number of jets, amount of pressure is critical for perfect entanglement.
This method allows the bonding of light and heavy webs of even up to 3-4 layers of natural or synthetic fibers.
Hydroentanglement has a wide range of application areas such as in wetlaid, wetlaid-spunlace, spunlace, carded, crosslapped, spunlaid nonwovens.
KM-HydroJet is a piece of excellent equipment for the hydroentanglement process. It shines out with its changeable and configurable jet heads per the application and customer needs, versatility, user-friendliness, ease of maintenance and reasonable ROI.