ITA Institut für Textiltechnik der RWTH Aachen University
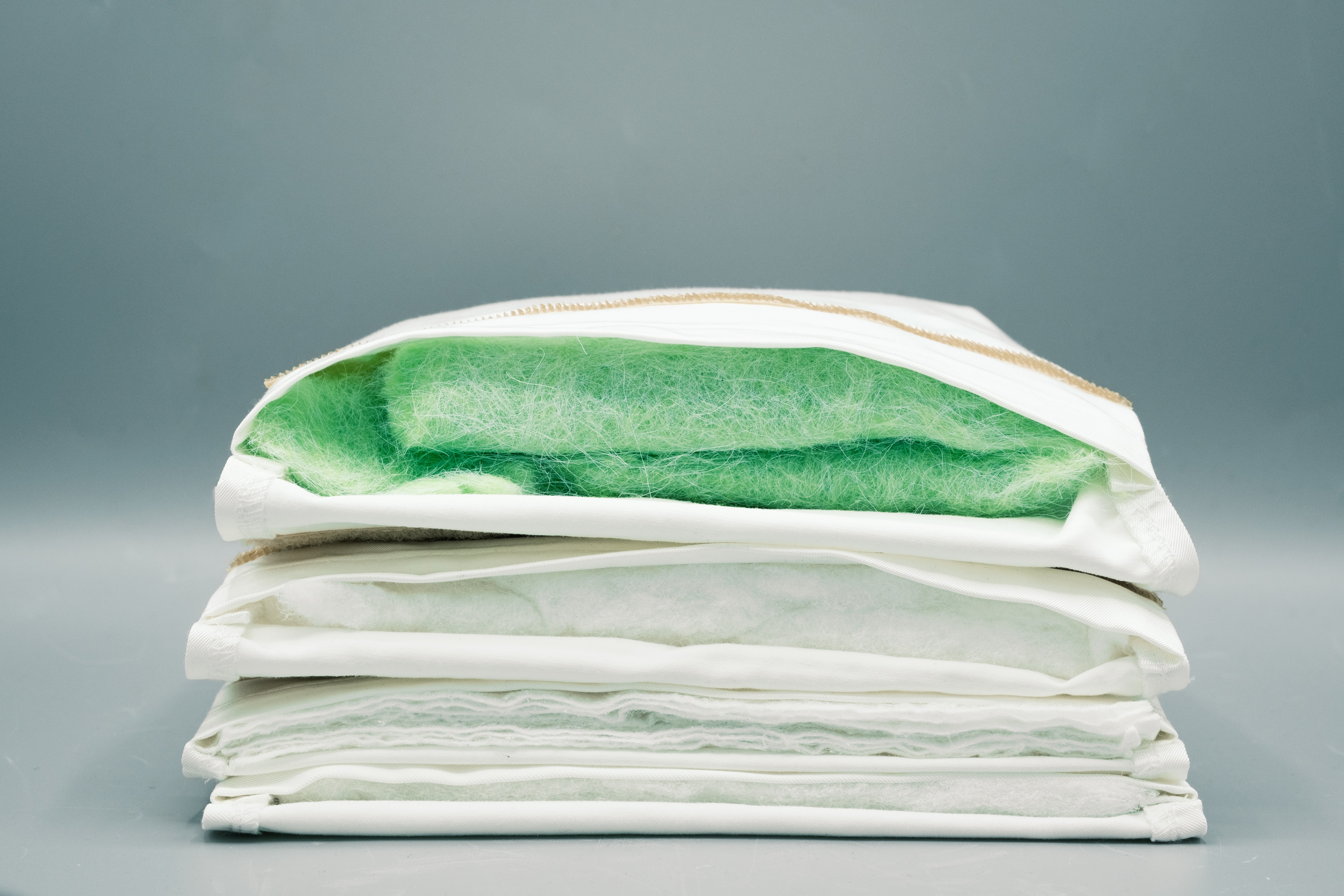
LIGHT LINING - Aerogel Fibres and textiles
Explore product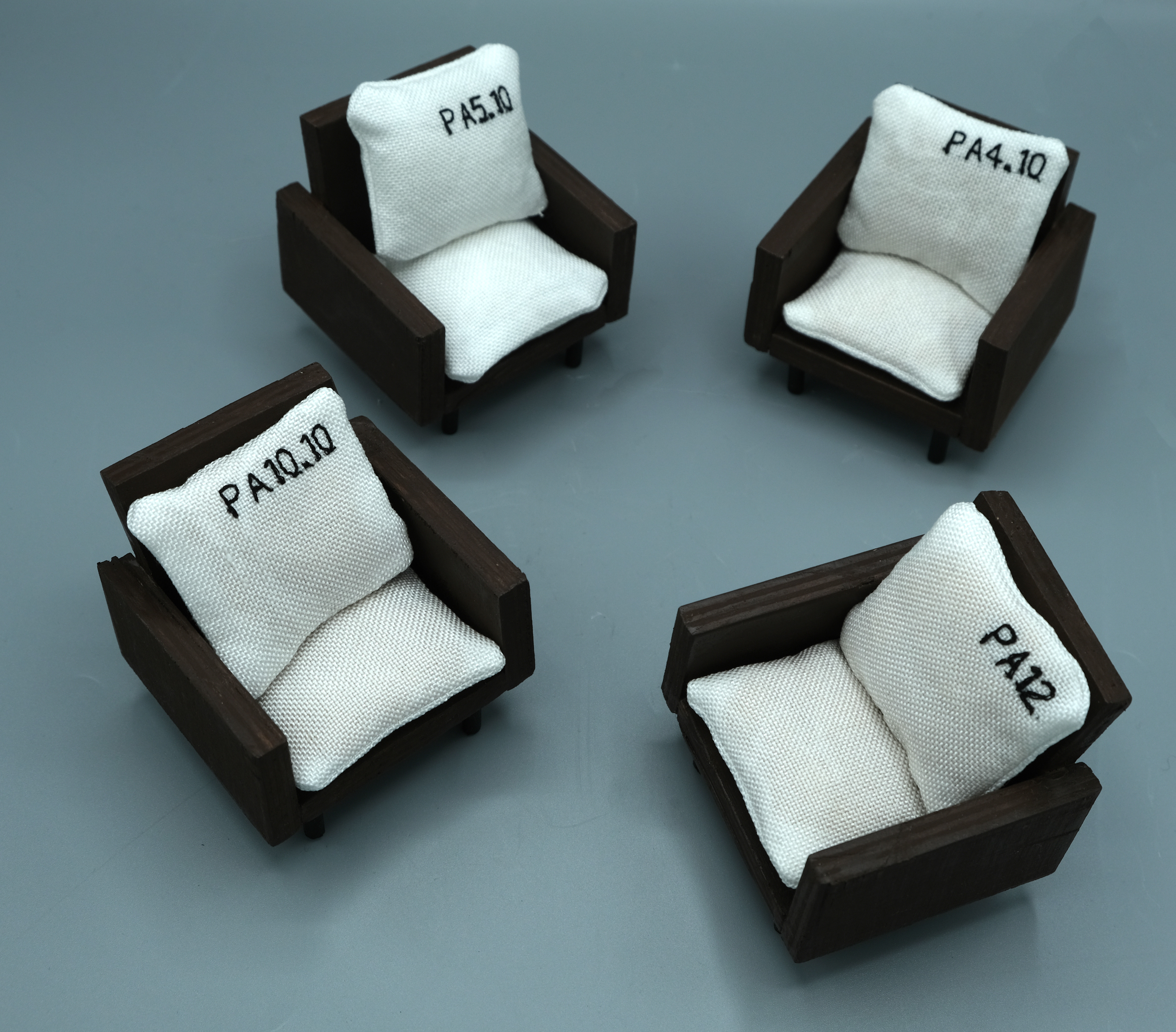
BIOBASE - Interior textiles made from biopolymers
Explore product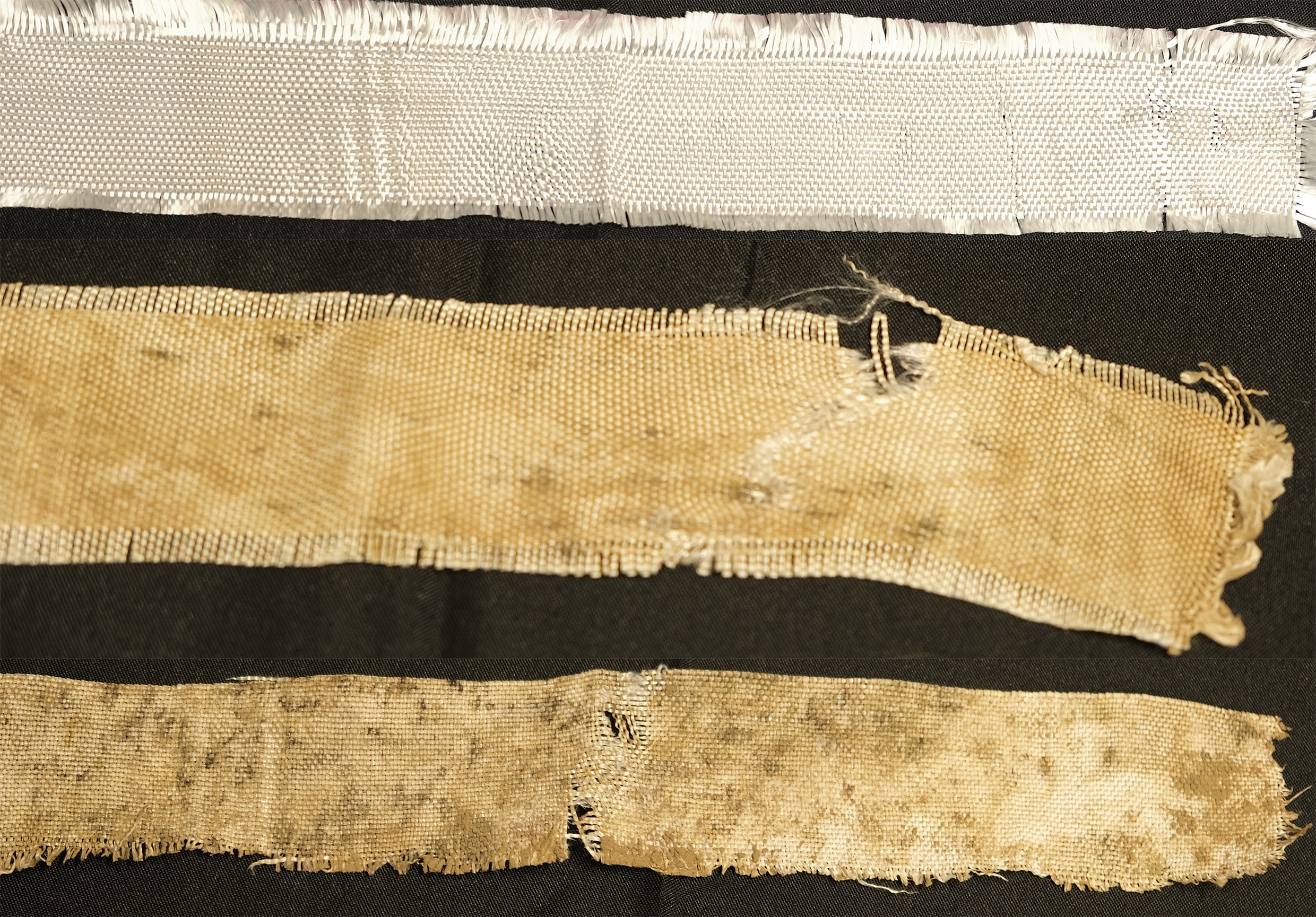
DEGRATEX - Biodegradable Geotextiles
Explore product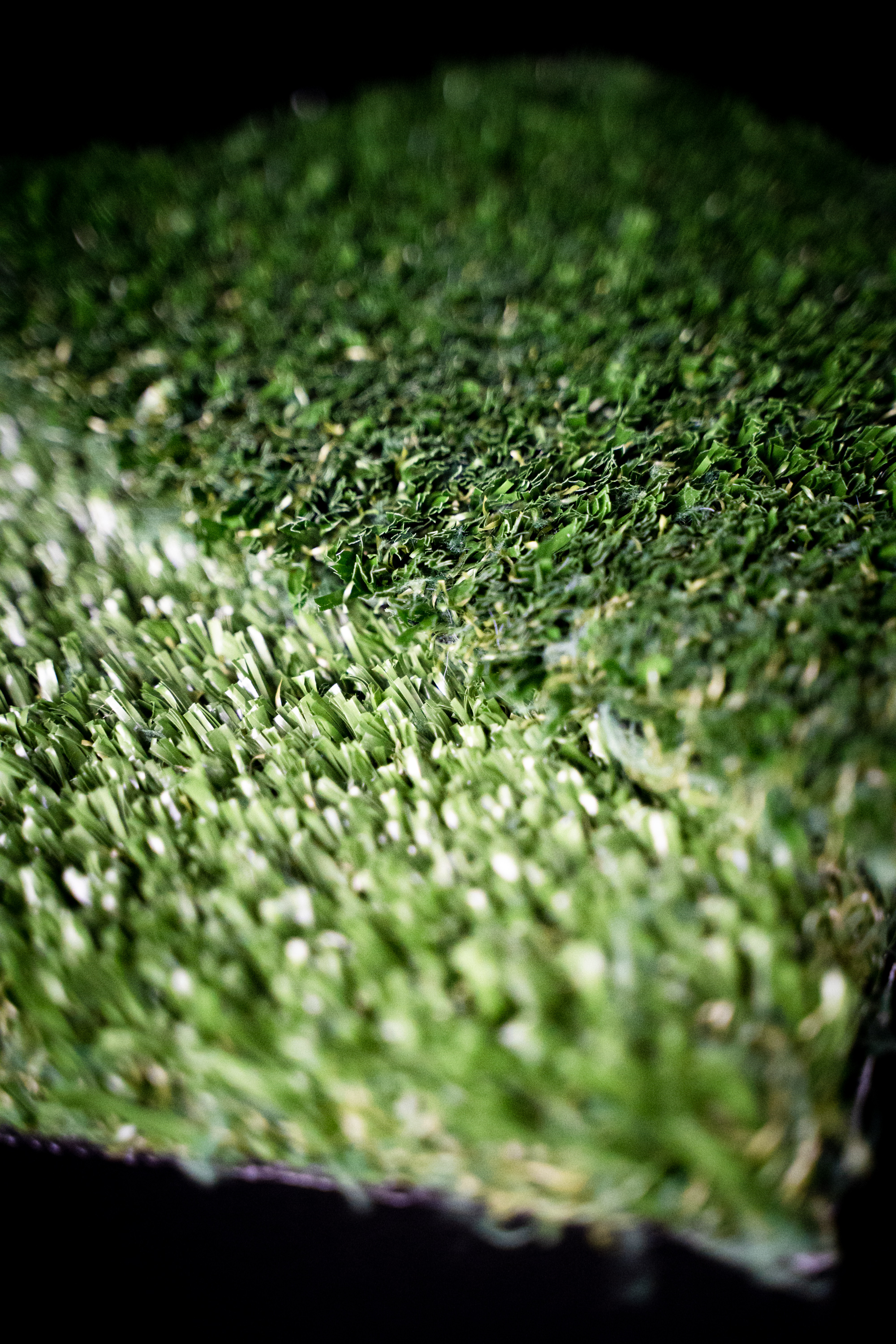
BIOTURF - The artificial turf of the future is „green“ again
Explore product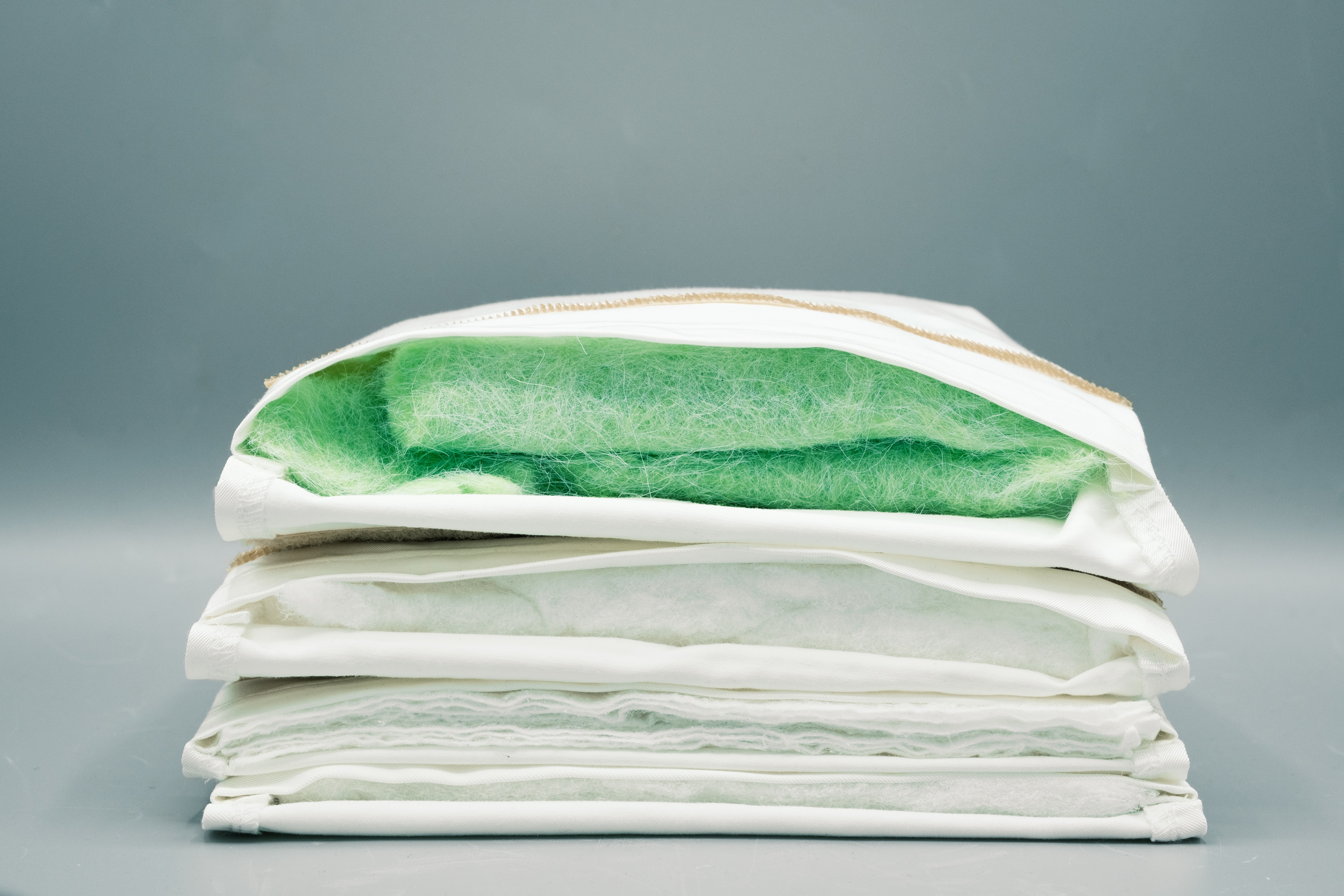
LIGHT LINING - Aerogel Fibres and textiles
Explore product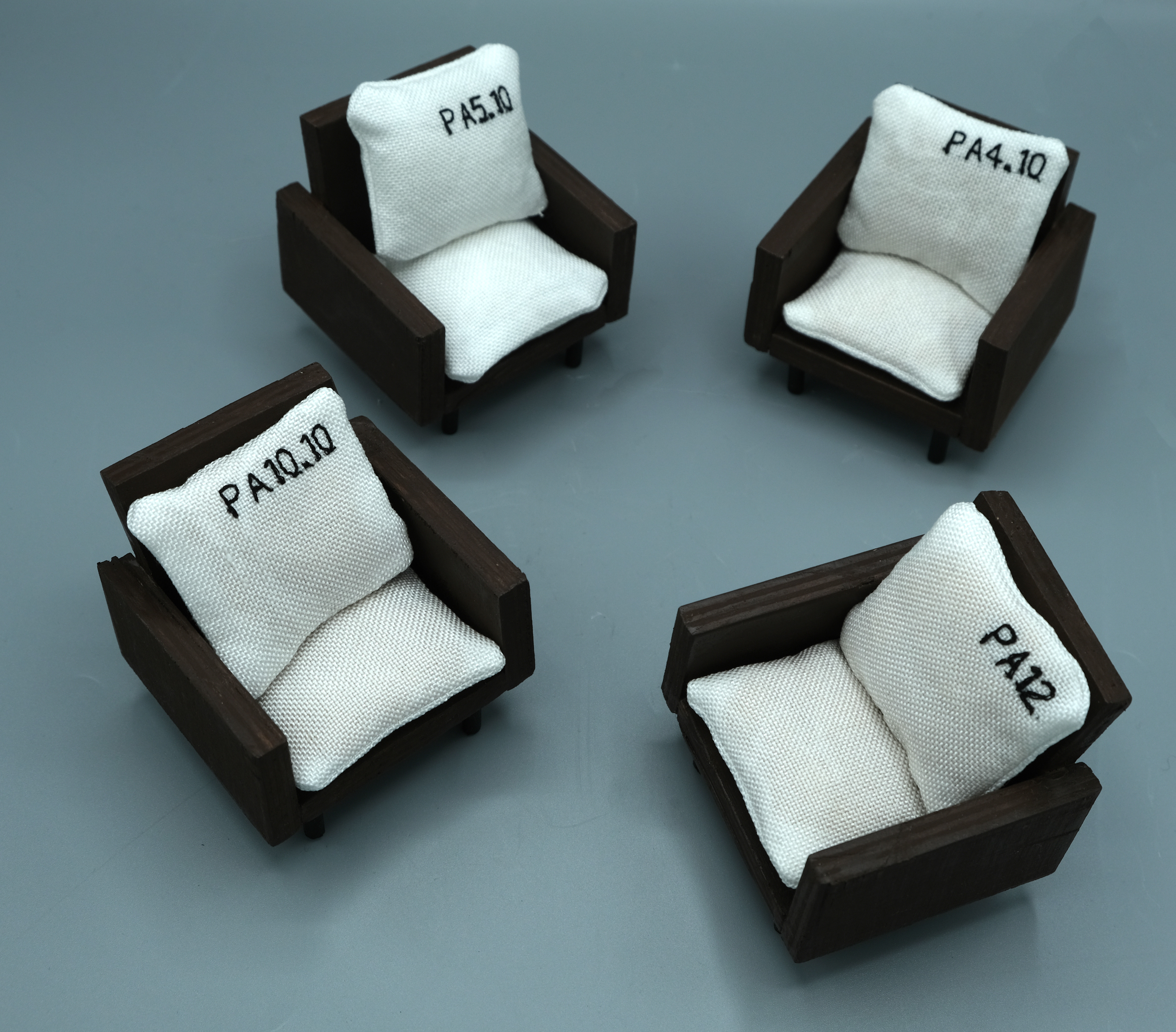
BIOBASE - Interior textiles made from biopolymers
Explore product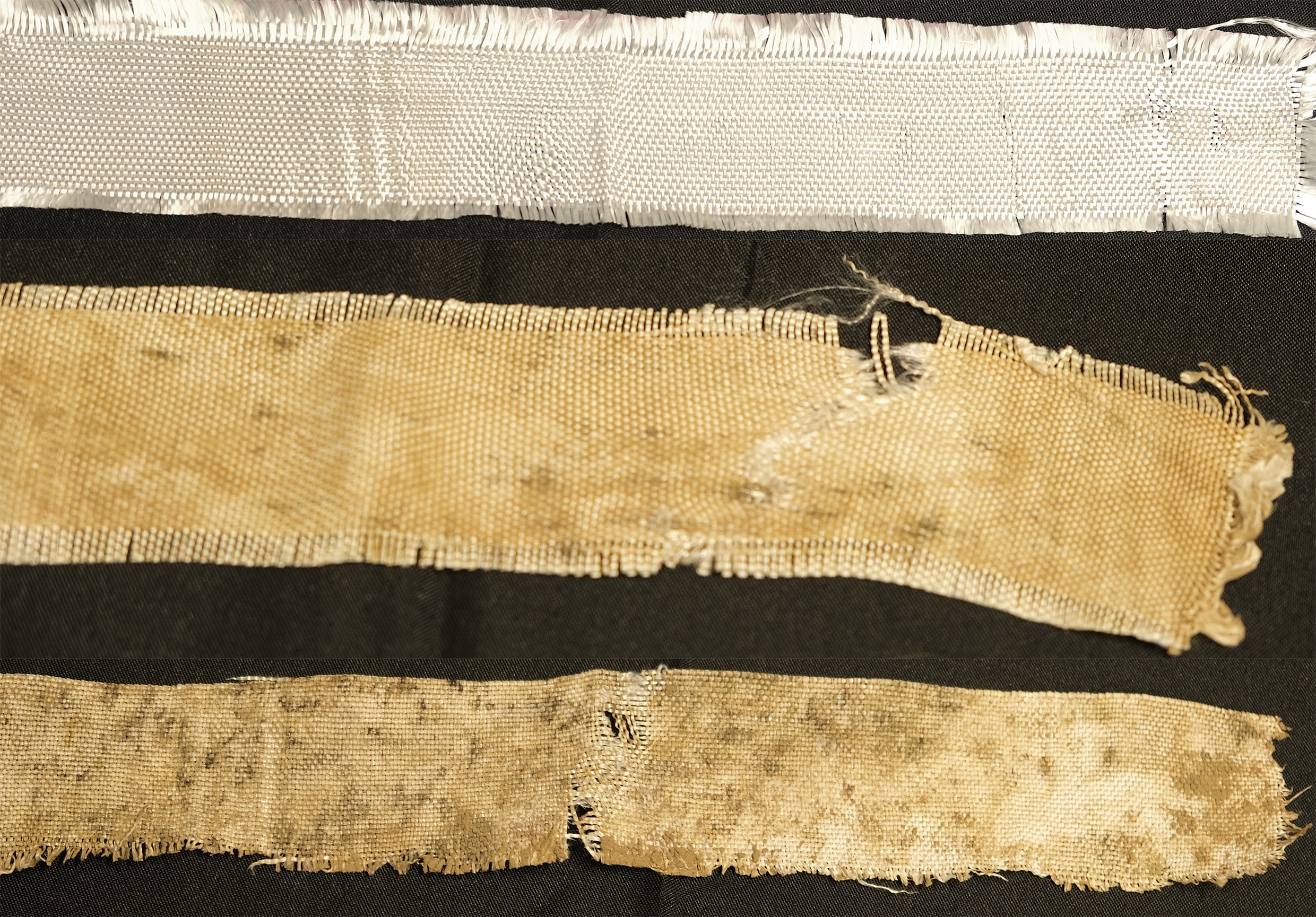
DEGRATEX - Biodegradable Geotextiles
Explore product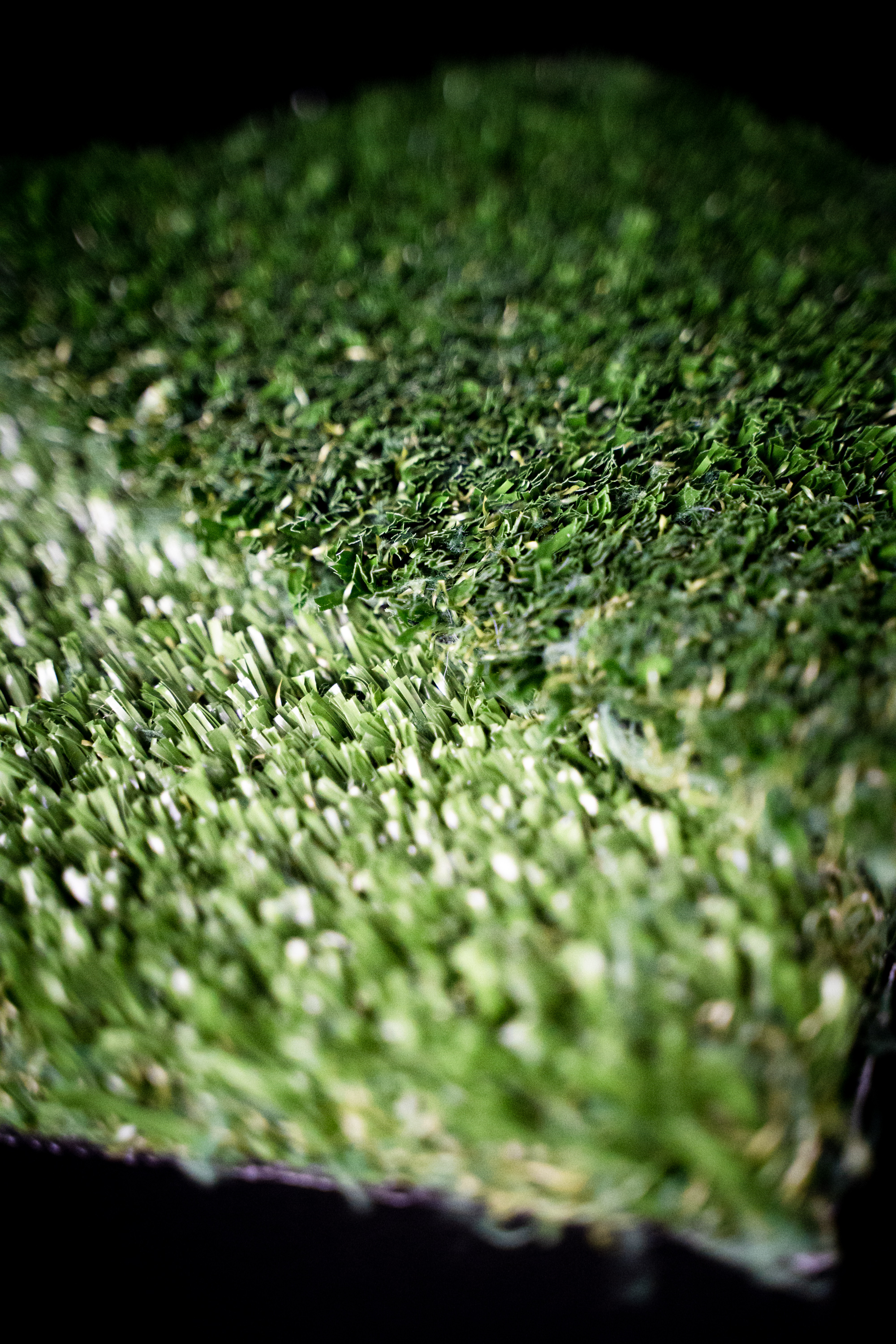
BIOTURF - The artificial turf of the future is „green“ again
Explore product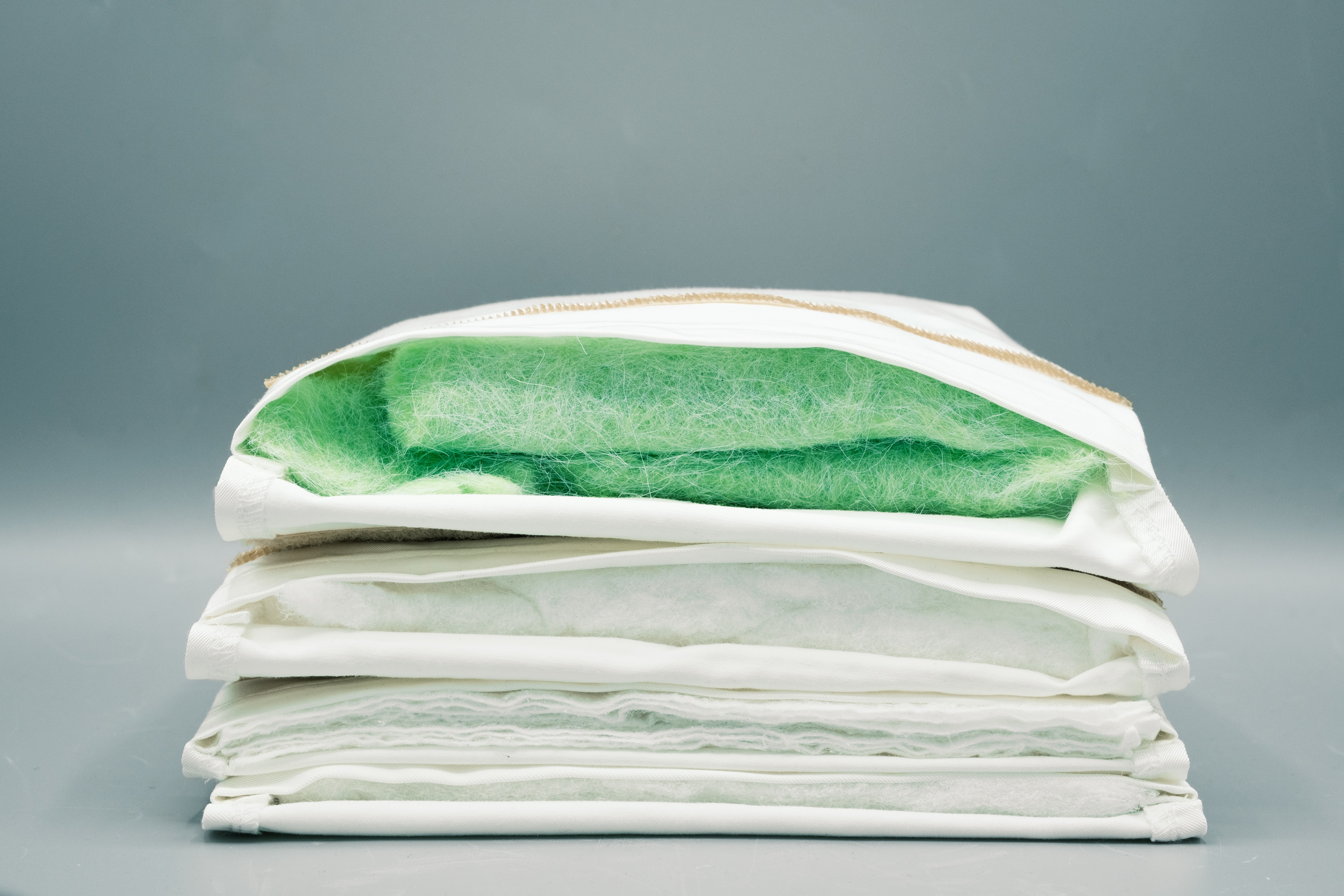
LIGHT LINING - Aerogel Fibres and textiles
Explore product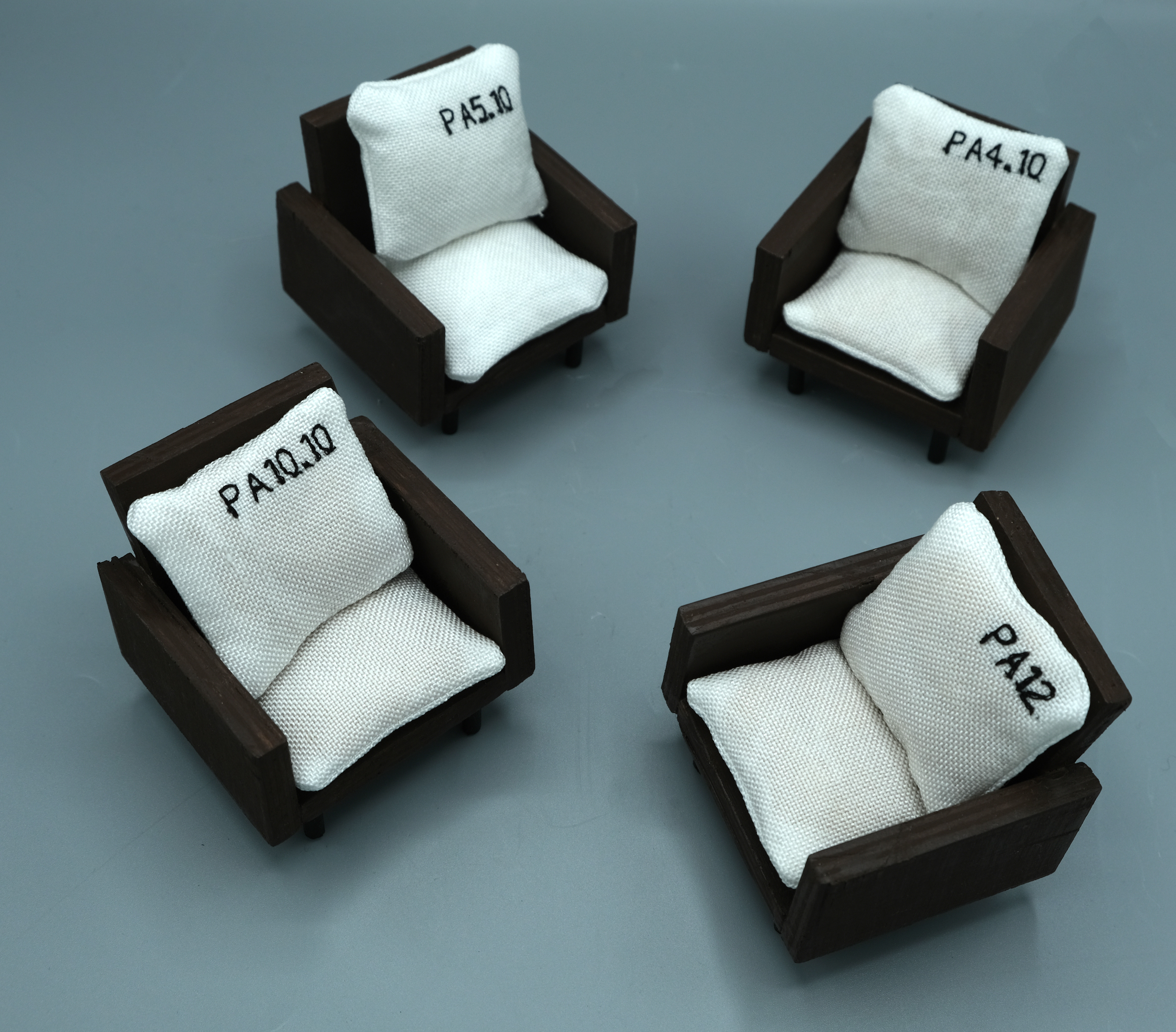
BIOBASE - Interior textiles made from biopolymers
Explore product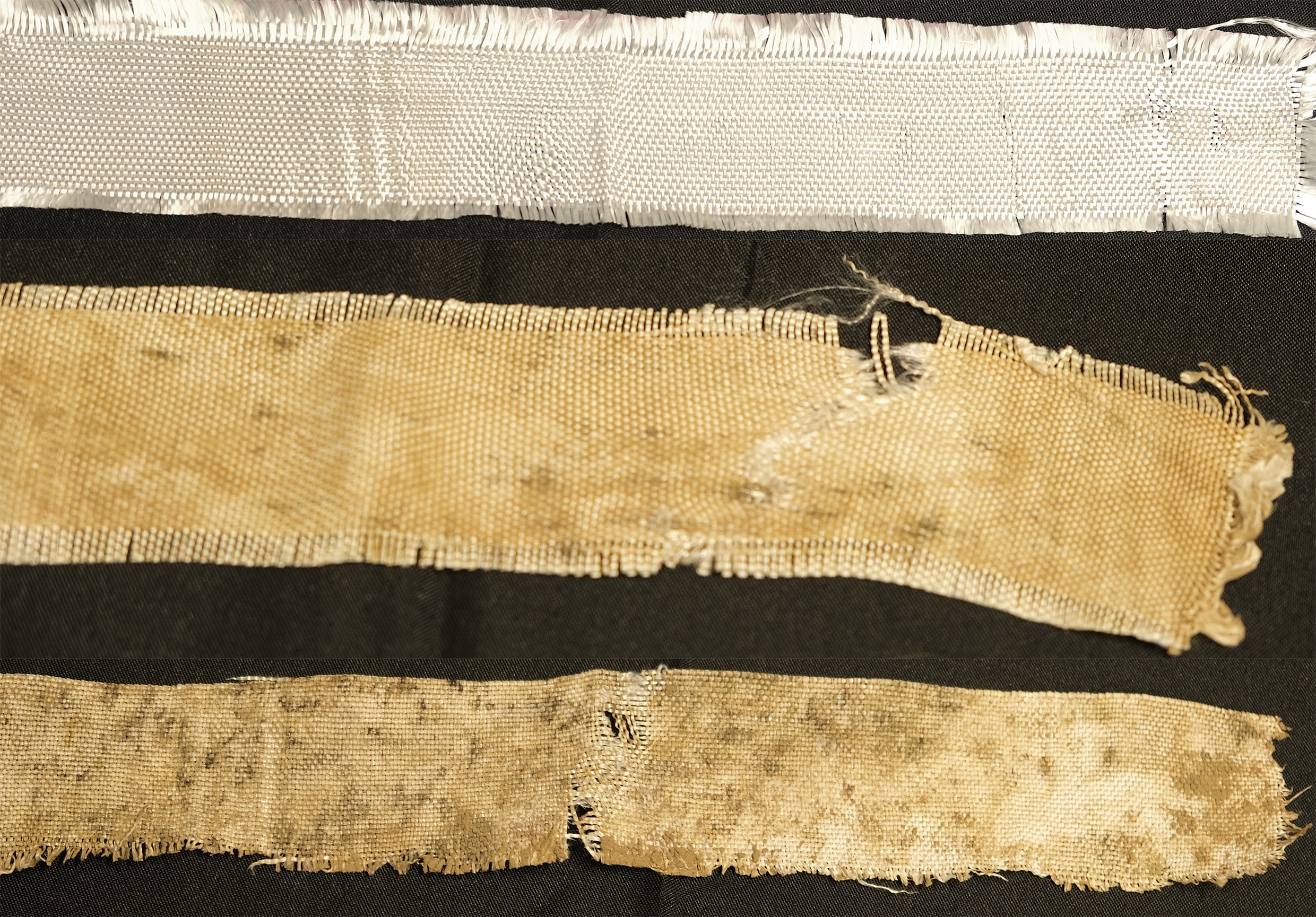
DEGRATEX - Biodegradable Geotextiles
Explore product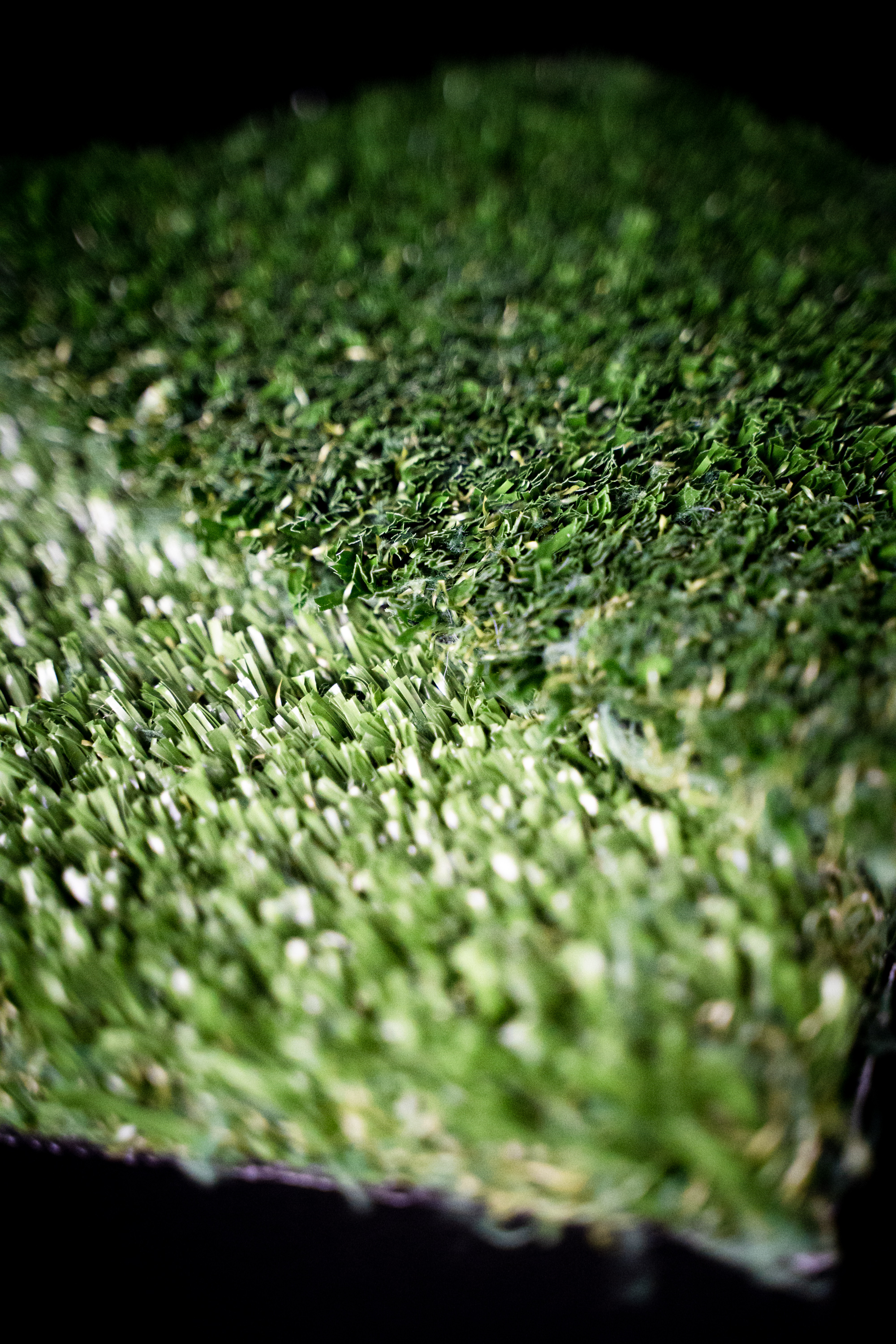
BIOTURF - The artificial turf of the future is „green“ again
Explore productAddress
ITA Institut für Textiltechnik der RWTH Aachen University
Otto-Blumenthal-Str. 1
52074 Aachen
Germany
Telephone+49 241 8023400
Fax+49 241 8022422
Discover more from us
About us
Textile Innovations
Sustainable.Digital.Individual
The ITA Group
The ITA Group International Centre for Sustainable Textiles focuses its core competence on the goal of ensuring the holistic biotransformation of textile technology and thus the use of biological principles for small-scale value-added processes. The ITA Group International Centre for Sustainable Textiles is an international research and training service provider for fibre-based high-performance materials, textile semi-finished products and its manufacturing processes with about 350 employees.
The core of the ITA Group, located in Aachen, comprises of the research and teaching institution Institut für Textiltechnik of RWTH Aachen University and the ITA Technology Transfer GmbH.
- The Institut für Textiltechnik (ITA) of RWTH Aachen University is the technological centre for textile engineering of RWTH Aachen University. The chair of textile engineering is a part of the faculty of mechanical engineering of RWTH. The institute is headed by the director Prof. Thomas Gries.
- The ITA Technologietransfer GmbH (ITA GmbH) in Aachen, headed by Markus Beckmann, is the technology transfer partner of the ITA Group. The ITA GmbH is an industrial service provider and commercialization group of the ITA group aligned with the previously mentioned research focus of the institute. The ITA GmbH offers the industry comprehensive solutions along the textile chain, accompanies the innovation processes from the idea to a commercially viable product launch, and supports the innovation process in diverse secondary industrial sectors.
Biotransformation of Textile Technology
Our goal is the holistic biotransformation of textile technology and thus the use of
biological principles for cycle-oriented value-added processes. This includes, for
example, the closing of raw material cycles, the reduction of energy and water
consumption for production processes and the principle of "Design for Recycling"
as a fundamental paradigm of product development.
Digitisation and Artificial Intelligence (AI)
Digitisation is an important tool in this context. The highly fragmented value
chain with many individual processes is networked and digitally mapped. Based
on the paradigms of Industry 4.0, the implementation of AI use cases, digital
business models and data-based networking along the value stream is
the new challenge.
Our Key Topics
Textile materials and semi-finished products are enablers for sustainable
products in all areas of life. Our research and development is oriented towards the
following key topics:
- Mobility
- Communication
- Health
- Building and living
- Resource efficiency
The design of innovative, digital workplaces and the development of new qualification
formats are also in our focus.
Profile of the ITA Group:
- Our key focus areas are based on social megatrends and challenges: mobility, health, energy, building and living, information and communication technology, materials, production, qualification
- We combine our wide range of technical knowledge through complete process chains with a thematic depth in selected technologies and areas of competence
- We use integrated engineering competencies: quality management, project management and process control, material analytics, modelling and simulation of processes and materials, manufacturing engineering, construction, product development
- We work on technology-exceeding, holistic questions: human-machine interaction, qualification, design and assessment of technology impact, industrial engineering and value chain management
The ITA Group: Our Value Proposition
Providing our customers with advanced, competitive, state of the art solutions through our 4 I’s
- Integrated Approach: The ITA is a ‘one stop shop’ for all textile based Solutions. The ITA strengthens its customers’ market position by providing advanced state of the art solutions.
- Interdisciplinary: All disciplines of a technical elite university are represented at the ITA
- Industry-oriented: Approx. 30 % of all ITA’s projects are direct industrial projects, while a further 40% are co-operation projects with the industry. The ITA is an extended, direct R&D team for industrial partners and an innovative service provider.
- International: Worldwide co-operation with prestigious universities and companies, focus point regions are Turkey, Asia (Japan, South Korea, and India), Russia, Europe, North America.
Our product groups
- Research, Development, Education, Consulting
- Fibres and Yarns
Our application areas / Solutions
More about us
Special Interests
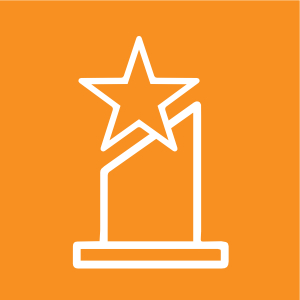
Our Brands
BIOTEXFUTURE - BTF
Recycling Atelier by Institut für Textiltechnik Augsburg gGmbH

Downloads
Keywords
- Circular Economy
- Smart Textiles
- Automobil
- Composites
- Nonwovens
Our Products
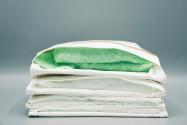
LIGHT LINING - Aerogel Fibres and textiles
Insulation materials are used in almost all areas. Today, they are often made from non-sustainable materials such as polyester, glass wool or foams. In most cases, these products have to be disposed of at great expense and are difficult or impossible to recycle. The use of bio-based aerogel fibre insulation materials should help to make a wide range of applications more sustainable and thus reduce the overall carbon footprint of the product while increasing its insulation performance.
Aerogels are highly porous materials that can consist of 99.8% air and therefore provide a high level of thermal insulation while minimising weight and material thickness. Aerogels therefore offer innovative solutions for a wide range of applications. In the textile and construction industries, for example, aerogels make it possible to minimise heat loss and thus improve the energy efficiency of textiles and buildings. To date, aerogels have primarily been produced in the form of inorganic sheets (so-called monoliths) or as a fabric coating. The disadvantages of these aerogel products are that their production processes are very resource-intensive and time-consuming and they are difficult to handle and process due to their brittleness. In addition, they are only recyclable to a very limited extent, making them unsustainable overall. To date, aerogel-based insulations have been niche products, as they cannot compete with conventional insulations in terms of price. The ITA has succeeded in developing a cost-effective and industrially scalable manufacturing process for insulating textiles made from 100 % aerogel fibres. Cellulose aerogel textiles are not only sustainable, but also very flexible and drapable compared to conventionally rigid or brittle aerogel products, which means that they can also be processed on conventional textile machines. The development at the ITA promises a new, globally unique, sustainable, highly efficient insulation material that combines the advantages of textiles (flexibility & good processability) with those of aerogels (very low weight & very good thermal insulation).
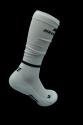
CO2TEX - Lifestyle compression stocking with TPU yarns that contain CO2, among other things
Elasticity is the ability of a textile to stretch or recover when required. This has a direct effect on functionality. Currently, elasticity in textiles is almost exclusively provided by so-called "elastanes".
Elastanes are elastic filament yarns that are usually made from fossil-based elastomeric polyurethanes. The estimated production volume is around 1.22 million tonnes per year. The elastomeric character requires the use of dry spinning technologies for yarn production, which leads to challenges such as low production speeds and therefore comparatively expensive yarns.
In addition, potentially hazardous and environmentally harmful solvents must be used - an appropriate occupational safety concept is therefore essential. At the end of the product life cycle, dry-spun elastanes impair recycling because the individual components of the textile cannot be separated with technically and economically justifiable effort. These challenges can be solved by using elastic, bio-based or CO2-containing TPU filament yarns.
In the CO2Tex project, TPU yarns were developed on industrial melt spinning systems using polymers with a renewable content of up to 18 per cent by weight. With elongations of up to 600 per cent, diverse and innovative applications can be developed, such as the lifestyle compression stocking exhibited here.
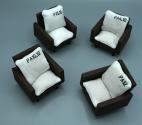
BIOBASE - Interior textiles made from biopolymers
A key problem in the production of man-made fibres based on synthetic polymers is the dependence on fossil raw materials, which are subject to various ecological and, in the long term, economic and political risks due to their finite nature. Polymers based on renewable raw materials represent an alternative. To establish biobased polymers in the textile industry and to demonstrate their full potential is the aim of project BioBase. The cooperation between research institutes and industry partners runs through the complete textile value chain of the respective benchmark products to develop viable biobased alternatives. Industrially produced demonstrators for four key sectors of the textile industry in Germany (automotive, sportswear, interiors and geo) are being created to demonstrate the potential of the biobased polymers available on the market.
As part of the BioBase project, which is funded by the Federal Ministry of Education and Research, interior textiles made from biopolymers are being developed together with Krall+Roth Produktions GmbH. In order to investigate the substitution potential of different biopolymers, an established, petroleum-based product is being modelled with polymers based on renewable raw materials. Therefore, commercially available bio-based polymers are selected, melt-spun into filament yarns, then air-texturised and further processed into fabrics. The manufacturing processes and machine settings along the textile value chain must be adapted to the respective material behaviour of the biopolymers. Using this process, fabrics made from four different (partially) bio-based polyamides were successfully realised for the interior sector.
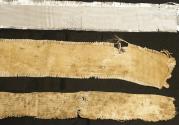
DEGRATEX - Biodegradable Geotextiles
The aim of DEGRATEX is to develop bio-based, degradable solutions for geotextiles for short-term applications such as the temporary stabilisation of earth structures or vegetation protection. The materials fulfil their function until they can be taken over by natural components such as soil-stabilising or ground-covering plants.
As part of the project, various materials and textile structures for these applications are being researched and the effects of the degradation process on the surrounding environment are being scientifically assessed. In addition, the project aims to develop assessment and decision-making tools for the use of degradable geotextiles. The results will make it possible to replace conventional geotextiles with bio-based and degradable product solutions within a technically and ecologically sensible framework. In this way, material structures can be used resource-efficiently in applications, provide added value from a technical and functional point of view and reduce the use of petrochemical plastics for use in nature.
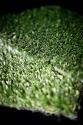
BIOTURF - The artificial turf of the future is „green“ again
Our objective is to develop an artificial turf structure made of bio- polyethylene (PE) similar to petroleum-based PE in terms of its key properties, with a mono-material structure to enable high- quality material recycling. Moreover, the new artificial turf structure will not require the addition of polymer infill granulate, thus solving the current microplastic challenge of artificial turf pitches.
Nowadays, communities and local authorities increasingly deside to construct artificial sport turfs instead to natural one due to low-maintainance efforts. Compared to natural turf, they offer an intensively usable, weed-free and weather independent surface that does not need to be watered or fertilized and require a minimum of personnel care.
On the other hand, the raw material feedstock, the structure and the application of microplastic infill granulate, to provide appropriate playability, cause various challenges. Thus, the multilayered structure of artificial sport turfs, consisting of various components, is usually based on fossil raw materials. In addition, the variety of materials in the pile and base layers or the backing layer are difficult to be recycled, and finally, microplastic infill material risks to be released into the environment due to rain, wind and further weather condition, Once released, the microparticles are non-degradable and therefore create a significant environmental pollution.
Due to this high environmental risk, the EU will ban „intentionally added microplastics“ i.a. for the construction of artificial turf pitches all across the European Union in the upcoming years.