IST, Industrielle System Technik Michael Haasner GmbH & Co. KG
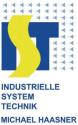
Address
IST, Industrielle System Technik Michael Haasner GmbH & Co. KG
Siemensstr. 20
47608 Geldern
Germany
Telephone+49 2831 977720
Fax+49 2831 9777222
Discover more from us
Follow us on
About us
May we introduce ourselves . . . ?
Electric control systems for textile and carpet plant, particularly the construction of multiple-motor continuous plants, are a highly specialised field for which today very few users and increasingly fewer manufacturers retain the necessary expertise within their
own company.
Standard practice is to have complete systems produced by a specialist workshop as a so-called "extended workbench" within the framework of outsourcing, After 25 years of professional experience at the firm Eduard Kiisters in Krefeld, where he worked as a chief designer responsible for the field of electrical engineering and the marketing of textile and carpet plants, it was precisely this trend which induced Mr Haasner to found the company "Industrielle System Technik" - or IST for short - in the year I998.
We offer individual tailor-made solutions to both plant manufacturers and users alike. Our switch cabinets can be equipped with state-of-the-art frequency inverters and programmable logic controllers (PLC). Our profession involves the modernisation of existing plants, the planning of new projects and expansions to old systems.
Our tasks include:
planning of the electrical control system
switch cabinet construction
PLC programming
visualisation (user interface)
complete installation of plants
commissioning
production monitoring
maintenance (online service)
With our qualified team we also offer our customers a 24-hour service by agreement.
During the period from 2005 to 2008 the I S T company was the main supplier to the firm Eduard KUsters in Krefeld / Zittau (EKK) and responsible for project planning (CAD, PLC programming and creation of the visualisation system) and the manufacture of the switch cabinets, as well as for the commissioning of the electric and pneumatic control system on the end-customer's premises.
Our customers from the electrical engineering, textile and carpet industry see us as a competent, flexible and reliable partner. We would be very pleased to be able to present our company and services to you in greater detail during a personal discussion. We are able to provide you with an all-inclusive solution.
Electrical - Mechanical - Process Engineering
On the Internet you can find further information about our other products and work at
www.ist-haasner.de.
Our product groups
- Research, Development, Education, Consulting
- Technology and Processes
Keywords
- Spannrahmen / Stenter
- Retrofit
- SPS / PLC
- Automatisation / Automation
- Textilmaschinen
Our Products
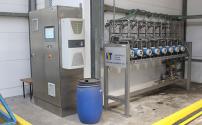
Metering station
Continuous metering
An automated metering station is used for the continuous feed of chemicals for dyeing and finishing. Up to eight different chemicals are metered into a padding bath, dyeing machine, or bleaching bath (Flexnip) in a bleaching plant.
The metering station consists of two parts:
- The control cabinet containing the entire control system
- The stainless-steel stand housing the metering pumps, transducers and flow meters
Consult IST beforehand if you intend to process other products or select other processing data.
Should you already be using a metering station with an older control system that you would like to upgrade, we can offer you a quotation for a new control system.
We would be happy to discuss the exact specification of the technology and its scope with you.
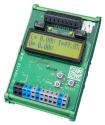
CVC-Modul 6.0
Our original CVC 1.0 module was developed at the beginning of 2000 with the function of evaluating the signal from our INKL 1.0 inclinometer. Over the years, the module has been developed progressively to the current version, CVC 6.0.
The Up and Down buttons are used for navigation to the individual menu items. The Select button is used to select the parameter (refer to the description of CVC 6.0).
Two relay outputs for the Min and Max range can be read into the PLC or integrated into the customer’s existing conventional control system.
Contactless tracing of a compensator roller
The traditional detection of the compensator roller position with continuous plants is carried out by means of the magnetoresistor potentiometer (FP). This FP is connected with the swinging axle in a given determined ratio of transmission by means of toothed belt or chain. lmportant mechanical energy is used to transmit the electric signal in function of the position of the compensator roller (PW) to the control. 2 signalling lines have to be drawn to each magnetoresistor potentiometer. The first one is needed to detect the voltage signal and the second one to detect the final positions of the compensator roller (above/below). lf the machines are still new and the compensator rollers have been adjusted correctly, the plant functions without any problems.
During later after sales-service works, often problems occur with the exact adjusting of the limit switches or the normal route of the potentiometer. ln addition, mechanical sources of error may arise (i.e., wear of the connection between the magnetoresistor potentiometer and the compensator roller), which may lead to a false signal transmission. All these problems can be avoided with our new inclinometer owing to the fact that it is directly mounted on the swinging axle. When moving the compensator roller, the axle rotates and the output signal changes. The inclinometer converts an angle of +/- 45° (0...90°) against the vertical axis into a linear proportional voltage. The inclinometer case is made of special steel and can be used in the photographic-, dyeing-, oil-, soap-, paper- and textile industry. One signalling line is sufficient for detecting the voltage signal.
Up to now this voltage signal could only be evaluated in connection with an SPS. From now on, you will be able to evaluate without SPS by means of our new electronic card the constant voltage signal in function of the line speed. This card has been specially designed to retrofit old plants. With a distribution voltage of 24V D.C. the card can be retrofitted into all switchboards. The detection of the final position of the compensator roller is pre-optimised on the electron- d ic card so that inside the switchboard the monitoring of the compensator roller can be directly involved into the control.
ln case of a new assembly the wiring of an additional line for the limit switches is not necessary. Thus, you can save time and money when using our new components. Of course, you can also evaluate other signals by means of these components as, for instance, with the loop control of a carpet range at the run-in ,,Steamer". Here, too the signal is detected and converted such that it directly controls the sequential drive.
When using our products the susceptance to trouble is decreased and the reliability of operation is increased which results in a better availability of your plant.
Control construction for system concepts
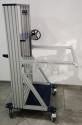
Mobile centre winder
Centre winders are used at the entry or exit of a textile, paper or carpet production system.
Fixed (stationary) winders and mobile winders are used for the various applications on the systems.
A further distinction is drawn between centre unwinders and centre rewinders.
Stationary winders are fixed to the floor; mobile winders can be moved to different machines as required.
Two different control system types are possible for use with the winder:
- Torque control
- Dancer roll position control
Please contact us to discuss the system and application for which you require the centre winder.
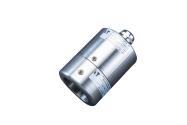
Inclinometer 1.0
Inclinometer 1.0
The inclinometer converts an angle of ± 45° (0 – 90°) to the vertical axis into a linear proportional voltage.
The housing of the inclinometer is manufactured from stainless steel (DIN X 12 CrNiS 18 8) and can be used in the following industries:
- Photographic industry
- Soap industry
- Paints and dyes industry
- Paper industry
- Oil industry
- Textile industry
The inclinometer is mounted directly on the centre of rotation (30/40 mm diameter shaft) and fixed with a recessed hexagon-head grub screw. It can be fitted without the use of a torque arm or other mechanical tools. The sensor cable is connected by means of spring-type terminals.
The sensor runs on ball bearings and is damped with silicone oil. It can be used in drive systems to detect the dancer roll position on textile, carpet and paper machines. Owing to its robust construction and full encapsulation, the inclinometer is completely maintenance-free and can therefore also be used without limitation in parts of an installation exposed to unfavourable ambient conditions.
Contactless tracing
of a compensator roller
The traditional detection of the compensator roller position with continuous plants is carried out by means of the magnetoresistor potentiometer (FP). This FP is connected with the swinging axle in a given determined ratio of transmission by means of toothed belt or chain. lmportant mechanical energy is used to transmit the electric signal in function of the position of the compensator roller (PW) to the control. 2 signalling lines have to be drawn to each magnetoresistor potentiometer. The first one is needed to detect the voltage signal and the second one to detect the final positions of the compensator roller (above/below). lf the machines are still new and the compensator rollers have been adjusted correctly, the plant functions without any problems.
During later after sales-service works, often problems occur with the exact adjusting of the limit switches or the normal route of the potentiometer. ln addition, mechanical sources of error may arise (i.e., wear of the connection between the magnetoresistor potentiometer and the compensator roller), which may lead to a false signal transmission. All these problems can be avoided with our new inclinometer owing to the fact that it is directly mounted on the swinging axle. When moving the compensator roller, the axle rotates and the output signal changes. The inclinometer converts an angle of +/- 45° (0...90°) against the vertical axis into a linear proportional voltage. The inclinometer case is made of special steel and can be used in the photographic-, dyeing-, oil-, soap-, paper- and textile industry. One signalling line is sufficient for detecting the voltage signal.
Up to now this voltage signal could only be evaluated in connection with an SPS. From now on, you will be able to evaluate without SPS by means of our new electronic card the constant voltage signal in function of the line speed. This card has been specially designed to retrofit old plants. With a distribution voltage of 24V D.C. the card can be retrofitted into all switchboards. The detection of the final position of the compensator roller is pre-optimised on the electron- d ic card so that inside the switchboard the monitoring of the compensator roller can be directly involved into the control.
ln case of a new assembly the wiring of an additional line for the limit switches is not necessary. Thus, you can save time and money when using our new components. Of course, you can also evaluate other signals by means of these components as, for instance, with the loop control of a carpet range at the run-in ,,Steamer". Here, too the signal is detected and converted such that it directly controls the sequential drive.
When using our products the susceptance to trouble is decreased and the reliability of operation is increased which results in a better availability of your plant.