Sicam S.r.l. Societa´Italiana Costruzioni Aeromeccniche
Address
Sicam S.r.l. Societa´Italiana Costruzioni Aeromeccniche
Via Selvanesco 57
20141 Milano
Italy
Telephone+39 02 826 6081
Fax+39 028266270270
Discover more from us
Follow us on
About us
SICAM manufactures machinery and complete plants for the textile, nonwovens and glass fiber, using its more than half a century experience in this sector according to the most advanced technological solutions and recent innovations.
SICAM core business are thermobonding and thermosetting heat processes and production range includes: Felt and Wadding Thermobonding Oven, Spun Bond and Spun Lace Perforated Drum Dryer, Stenter Frame, Calender, Abrasive Wadding Multi Layer Oven, Textile Dryers, Glass Yarn and Glass Fabric Dyer and Glass Fiber Chopped Strand Mat Plant.
The methods of projects implementation are continuously improving, that allows us every year to offer complete plants and machinery with technological innovations and high quality standards, thanks to an active involvement in an international sector in constant evolution.
THERMAL INSULATION, SOUND PROOFING AND BUILDING ›
THERMAL INSULATION, SOUND PROOFING AND BUILDING; SHOES LEATHER GOODS; WIPES and CLEANING; AUTOMOTIVE INDUSTRY; CLOTHING; FILTRATION; HYGIENE/BODY CARE; MEDICAL; CIVIL ENGINEER / GEOTEXTILE; HOME FURNISHING; RESINS REINFORCEMENT;
Keywords
- Spun Lace
- Oven - Dryer
- Recycled Fiber Felt
- Spun Bond
- Turn-Key Plant
Our Products
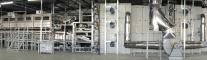
Recycled Fiber Felt or Wadding Thermobonding Line - Web Forming, Oven, Winding
This line is used for the production, from recycled fibers, of Insulation felts, Mattresses felts and Automotive felts.
The felt, from the airlaid or from the card/crosslapper, enters in the thermo bonding oven with or without needle punched treatment.
PPfibers or BicoPES fibers melt in the oven, bonding the felt. The final density is fixed in the calender and in the cooling section. Surface infrared treatment at the end.
FORMING UNIT
SICAM supply a pneumatic forming unit based on pneumatic formation.
The pressure feeding assures an high accuracy across the section and then an homogenous fiber web formation.
The particular design allows fibers disposition in S shape along the thickness and this disposition increases the mechanical performances of the materials.
This forming unit can be used as a card feeding system or for direct fiber web formation to feed ovens or other bonding systems.
- Pressurized forming unit.
- Very uniform batt formation system.
- It can be used as a stand-alone air forming system or as a feeding system for the following airlay cards.
- Precise weight control system with 6 loading cells and PID feedback system.
THERMOBONDING OVEN
Sicam has developed an high efficiency air through ventilation and a reliable adjusting of the ventilation width( according to the nonwoven width ), in order to avoid any side bypass of the process air during the air through ventilation. In addition we find the construction Sicam philosophy without sliding elements. this solution make possible an easy access and to inspect inside the oven reducing the maintenance time and costs.
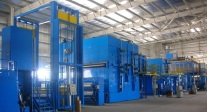
Spun Bond - Hygenical, Geotextile or Roofing
The Spun Bond process is gaining market quotes thanking to the process improvements to the advantages of the mechanical performances of the end products and to the reduction of the production costs.
From the experience of our customer, from our know how and our R&D, many palnts has been supplied with the satisfaction of the customers.
Main features of the plant are the advanced engineering and the flexibility according to the final product and to the polymers to be processed.
High productivity thanking to special bushings installed in single or double beams.
Maximum number of holes per length unit.
High speed plant with high productivity.
The plant can produce both PP and PES fibers.
The quality of the fiber is hight, due to theuniformity of distribution and isotropicity thanking to the distribution system in the forming section.
The Spoun Bond plant improuve or decrease the production cost, reducing the involved manpower and the maintenance time; the energy consumption is also reduced by the special air generation system with high recovery.
The modular design allows to supply tailor made installation without compromises.
Full compatibility for processing either PP or PET polymer; Possibility of use of PET flakesasan alternativeto PET chips;
Filament scooling and stretching, with indipendent positions and individual round ejectors, fed by low pressure air that guarantees operational continuity and stability of the filaments characteristics over time;
Balanced tensile strength ratio MD/CD.
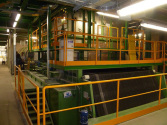
Glass Fiber - Nonwoven or Chopped Strand MAT
GLASS FIBER CHOPPED STRAND MAT
The sicam chopped strands mat plants are used for the production of nonwoven suitable for the resin reinforcement, for application in nautical field to make hulls and for the production of tanks and components in the reinforcement resin. Sicam proposes a plant formed by a formation unit where the glass yarns coming from bobbins are cut and evenly laid on a collecting conveyor, by an impregnation zone where glass fibers are impregnated by thermoplastic powder or urea formaldehyde in emulsion, by an oven which provides to the drying and thermosetting.
At the exit the glass web is calandered and trimmed before rolling.
FINISHING OF GLASS FABRIC
The Sicam for glass fibers finishing are used for the impregnation of the glass fibers with chemicals which make the fabric suitable for the reinforcement of different kind of resins as happens in the production of electronic cards.
Sicam proposes a plant composed by unwinding device with welding unit, accumulator, impregnation unit, vertical air impingement oven for drying and thermosetting, accumulator and winder at the exit.
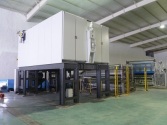
Spun Lace - Web Forming, Hydroentanglement, Drum Dryers, Winding
Complete lines for the production of Spun Lace nonwovens like cotton pads, wipes and light webs products.
After the forming section of the web, the water jet machine bonds the fibers on the hydroentanglement principle and a proper oven evaporate the water making the web ready for winding.
The web forming is obtained by traditional carding machine or airlay technology according to the final products.
The airlay system, suitable for low weights, the water jet, on the basis of a deep experience in Spun Lace technology, and the high efficiency oven, make the SICAM line reference point in Spun Lace production as reliability, innovation and efficiency.
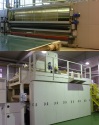
Continous Press and Calenders
CONTINOUS PRESS
The Sicam double conveyor continous press is suitable for the lamination, the surface finishing and the compression and so density increasing of nonwovens.
Sicam has developed a working principle based on a combination of heat and pressure. The Sicam double conveyor press is able to obtain a perfect smoothing effect on the surface, is able to laminate more materials ( also not permeable) by melting the fibers or with the help of powder or liquid adhesives, and is able to increase the material density in the nonwoven mixed with PP or Bico PES.
Sicam reaches the above results thanking to a machine which provides for the passage of the material in pressure between two conveyor belts in glass / Teflon between fist hot plates and then cool plates.
To produce different thickness between the heating zone and the cooling zone couples of calendar rolls are placed.
CALENDERS
The Sicam hot calendar can be supplied with two or three rolls, driven dried by a cardanic shaft system and independent motors and can be heated by:
- direct electric heating
- diathermic oil heated by electric resistance or gas boiler
In the calenders with oil heating system, Sicam uses high flow pumps which allow to keep at low level the temperature delta between the entrance and the exit of the oil from the rolls, to obtain a perfect temperature uniformity on the surface of the roll to obtain a top of quality nonvowen.
This temperature uniformity is obtained also thanking to the high speed oil circulation inside the roll in proper channels.
According to the company philosophy, Sicam carefully chooses the materials and the thermic treatment of the rolls of the machine according to the request of the technological process.
The rolls are built in a special steel which then after thermical treatment reach a very high hardness not only on the surface , but also in the deep thickness.