MMP Filtration Pvt. Ltd.
Address
MMP Filtration Pvt. Ltd. C3-602 Anushruti Towers, S.G. Road Thaltej
Ahmedabad 380059
India
Telephone+91 98300 30030
Discover more from us
About us
- Established in 2003, mmp stands as a pioneering force in the realm of yarn manufacturing within India, adeptly meeting the dynamic and exacting requirements of the nation's foremost textile weavers.
- Nestled in the heart of Ahmedabad, India, mmp Filtration boasts a state-of-the-art infrastructure equipped with cutting-edge technology, enabling the production of unparalleled quality yarns that embody a diverse range of coveted properties. Our extensive repertoire includes High Permeable Friction Yarn, Core and Sheath Yarn, Coated Yarn, Twisted Yarn, Fire resistant Yarn, Cut Resistant Yarn just to name a few and each meticulously crafted to meet the bespoke needs of our discerning clientele.
- At mmp Filtration, we pride ourselves not only on our superior products but also on our unwavering commitment to innovation, excellence, and customer satisfaction. With a relentless pursuit of perfection and a dedication to surpassing industry standards, we continue to set new benchmarks in yarn manufacturing, solidifying our position as a trusted partner for India's premier textile weavers.
- mmp Filtration is passionate about ushering in a new era of the technical textile with an extensive portfolio of innovative, high-value, and sustainable yarns.
- Our reputation in technical yarn manufacturing inspires us to always reinvent ourselves to create a competitive advantage. Strategic acumen, decisive management, and a dedicated team spun into the common thread of continuous innovation and consistent quality are certain to herald our leaps that will introduce new dimensions for making modern-day fabrics.
- mmp Filtration is the 1st – and at present the only – company to manufacture uniquely crafted Highly Permeable Friction Yarn.
- With over 18 years of expertise in technical textiles, mmp Filtration is the first producer of High Permeable Friction Yarn and Open End Yarn for technical textile applications. With an annual capacity of 3600 tonnes and a team of over 200 members, we are poised to continue our legacy of excellence and innovation in the industry.
Our product groups
- Fibres and Yarns
Our application areas / Solutions
Downloads
Documents
Keywords
- Core Spun Yarn
- Dref Spun Yarn
- coated Yarn
- Cut Resistant Yarn
- Fire Retardant Yarn
Our Products
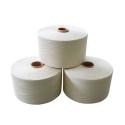
Open End Yarn
mmp’s open-end Yarn is a product of quality and innovation intertwined to create exceptional textile solutions. Open-end spinning is a high-speed method of yarn production, offering significant advantages in terms of efficiency and productivity. Our Open-End Yarn stands as a testament to our commitment to excellence, offering superior quality and versatility for all your crafting needs.
Making Open-End Yarn begins with selecting the finest fibers, which are carefully cleaned and prepared for processing. Through a series of precise steps, including carding to align the fibers, drawing to stretch them into thin strands, and roving to twist them together.
Open-end spinning can accommodate a wide range of fiber types, including natural fibers like cotton and wool, as well as synthetic fibers such as polyester and acrylic. The advanced spinning machines then use open-end technology to spin the roving into yarn without the need for traditional spindles. This innovative approach not only enhances efficiency but also ensures that each strand of yarn is uniform, durable, and of the highest quality.
Unlike traditional ring spinning, which produces one yarn at a time, open-end spinning can produce multiple yarns simultaneously. This increased throughput makes it well-suited for large-scale production environments. Additionally, open-end spinning often consumes less energy and resources, contributing to overall cost savings in production. The process often generates less waste and consumes fewer resources compared to traditional spinning methods, aligning with sustainability initiatives in the textile industry.
The versatility of mmp's Open-End Yarn knows no bounds. It's ideal for weaving and even various industrial applications. From finer use cases to coarser ones, these yarns have a variety of applications.
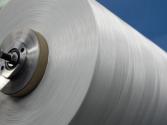
Coated Yarn
mmp leads the way in pioneering advanced coating technologies for filament and staple fiber yarns. Our expertise spans the entire spectrum of yarn treatment, coating, and drying techniques, meticulously customized to complement subsequent processes and various yarn applications.
The process starts with selecting the yarn base, including natural fibers like cotton, synthetic fibers like polyester or polypropylene, or nylon, or blends. The chosen yarn is thoroughly cleaned to remove any dirt or impurities that could affect coating adhesion.
A suitable coating material is chosen based on the desired properties and functionalities of the yarn. It can be in liquid form, powder, or chemical compound, often with tailored additives for specific applications like UV inhibitors or flame retardants.
The prepared yarn is coated using dipping, spraying, or padding methods. It passes through rollers or guides for uniform coverage. After coating, the yarn is dried or cured to solidify and bond the coating to the fibers. This may involve heat, UV light, or chemical reactions. After drying or curing, additional finishing processes may be applied to enhance the yarn's properties or aesthetics. This can include smoothing the surface, adding extra layers for durability, or sealing for environmental protection.
mmp's coated yarns elevate fabrics with water resistance and durability, spanning technical textiles, automotive, and industrial uses. From outdoor gear to Protective wear to home furnishings, our yarns offer safety, antimicrobial properties, and stain resistance. With yarn coating, each strand embodies durability, function, and style.
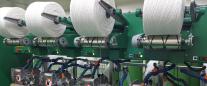
Dref Yarn
mmp is one of the leading integrated companies dedicated to manufacturing filter cartridges from start to finish, ensuring the highest standards in technical specifications and the advantages of our high-absorption filtration yarn. Filtration yarn, manufactured with Austrian technology of Friction spinning or DREF spinning and crafted under experts, is more cost-effective and efficient than any other yarn in the industry.
mmp yarn is made from either polypropylene or polyester, providing different properties suited for filtration. Polypropylene is often chosen for its chemical resistance, while polyester offers durability. The yarn is produced using Dref Friction Spinning technology, a method that uses friction to create yarn. This technology ensures the yarn has specific characteristics suitable for filtration applications. The output is pure yarn that has 20-40% more air volume. The increased cross-section diameter of this DREF spun yarn can soak more water than usual yarns.
mmp is the solo producer of absorbent bleached FDA class 1 device medical grade cotton yarn for highly sophisticated filter cartridges and offers a top notch polypropylene yarn with high anti microbial properties along with the FDA polypropylene yarn with low / zero foaming characteristics.
mmp Filtration Yarn comes in counts ranging from 0.4 to 1.0 Ne, providing versatility in thickness. The yarn fibers have a denier ranging from 1.4 to 6, contributing to efficient filtration. Conveniently wound onto spools weighing 4.5 to 6.5 kilograms, it offers ease of handling for various filtration applications.
The liquid exhibits higher permeability when passing through filter cartridges crafted with mmp's DREF spun yarn.Consequently, the filter's dirt-holding capacity increases, reducing the likelihood of low pressure. This advantageous feature contributes to achieving optimal output in industries such as Oil and Gas, Pharmaceuticals, Chemicals, Food, and Dairy, as well as Energy/Power.
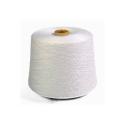
TFO YARN
mmp is one of the leading producers of Plied Yarn, known for crafting durable and long-lasting textiles. The method of twisting two or more single yarns together called doubling, folding, or ply twisting, is essential for satisfying certain textile requirements that cannot be fulfilled by single yarns. Yarns created through this process are designated as doubled yarn, folded yarn, or plied yarn, and the machines intended for this purpose are called doublers, ply-twisters, or Two-for-One (TFO) twisters.
Crafting of this yarn starts with two or more strands of yarn, known as singles, which are fed into a special twister machine. This machine twists the singles together, intertwining them in the opposite direction of their original twist. What makes plied yarn special is its Two-for-One twist, meaning each rotation of the twister adds two twists to the yarn.
This double twist enhances the yarn's strength and stability, making it less likely to break during use. Once twisted, the plied yarn is wound onto bobbins or cones and packaged for use in various textile applications. With plied yarn, you can trust in quality and reliability for all your crafting needs. mmp’s plied yarn is a powerhouse in various industries, prized for its unmatched strength and durability. In the apparel sector, it weaves its magic for innumerable applications in various End Products. Home textiles, like bed linens and curtains, benefit from its resilience, while industrial applications rely on its ruggedness for automotive interiors and protective gear.
Outdoor enthusiasts and athletes trust plied yarn for performance wear that endures harsh conditions. Even in furnishings, Plied yarn shines, offering sofas and cushions longevity and strength. In every application, Plied yarn delivers reliability and durability, making it a go-to choice for manufacturers worldwide.
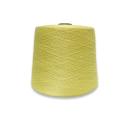
Aramid Yarn
Para-aramid spun yarn is made of para-aramid staple fibers or blended with other organic and inorganic fibers through various of processing technic.
Para-aramid spun yarn shows excellent performance on anti-cutting, flame-retarded, heat-resistant and arc-protection applications.
Features:
- Non-toxic, safe and human body friendly
- Heat and chemical resistance
- Flame retardant and fireproofing
- Cut resistance and electrical insulation