Bombi Meccanica S.r.l.
Address
Bombi Meccanica S.r.l.
Via Della Lora 38
50031 Barberino Di Mugello Firenze
Italy
Telephone+39 055 847 9351
Discover more from us
Follow us on
About us
Mario Bombi, a driven individual, founded the company in Prato, Italy in 1968, recognizing a demand for reliable, high-quality machines for textile finishing. With his innovative solutions, he quickly became an industry leader, passing the reins in a second stage to his capable childrens, Riccardo, Tancredi, and Lucrezia. The company, now named Bombi Meccanica, specializes in finishing machinery for nonwovens, boasting a diverse range of products. In 1994, we expanded to a new facility in Barberino, enhancing efficiency and productivity. With the third generation now involved, Bombi Meccanica employs over 30 staff and serves clients worldwide. We focus on personalized solutions, ensuring customers satisfaction and continued growth, always remaining a business in the hands of the family. Our product lines includes thermobonding ovens, double belt presses, hot calenders, perforated drum ovens, end of line with different solutions of cutters winders and automatic pad stackers. Also we produce accessories machine like foam generators , coating heads, foulards. Our success lies in their commitment to understanding and meeting each customer's unique needs, studying and developing ad hoc solutions for different scenarios. Lately we have been involved in processes of recovering textile waste transformed into innovative products capable of giving a second life to what was destined for destruction or landfill.
Our product groups
- Technology and Processes
Our application areas / Solutions
Keywords
- Calenders
- Double belt press
- Perforated drum oven
- Cutting machine
- Ovens
Our Products
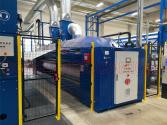
HOT CALENDERS
HOT CALANDER
A hot calender is the simplest and most effective solution to transform a standard needled punched felt into a high technical product, giving immediate benefit and extra added value. This is achieved without any modification within the existing line.
Typically a calender is installed in-line, directly after the last needle-loom, but it can be installed off-line in order to serve more than one producing line (Calender working speeds are faster than a standard felt production line)
In one single step, calenders are able to make an excellent finishing job to the felt, with the following advantages:
- Calibrating accurately the product to the required thickness;
- Increasing the mechanical properties, by thermofixing the fibers;
- Reducing the peeling effect;
- Reducing transport costs (up to 60 - 70%), by reducing the roll diameter of the final roll.
Special model for embossing of the felt.
-Rolls surface chromed or hardened
-Independent temperature for each roll
-Cooling rolls in exit
-Rolls diameter up to 800mm
-Rolls width up to 7100mm
-Parameters control via plc and operator panel
-Working pressure up to 150t
-Rolls bending compensation from control board
-Rolls heated with thermal oil circulation
-Oil heated with electric or gas fired unit
-Upper hood for smoke removal
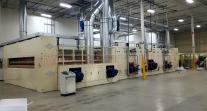
OVEN
THERMOBONDING OVENS
Re-designed and improved, the new thermobonding oven finds its application for all products : Natural fibers webs with high thickness, polyester wadding high loft, technical products, wood fibers, any kind of recycled fibers. Ventilation is forced from top to bottom or bottom to top, reversible in each section. Lateral closing of the air, from control panel. Heating with industrial direct gas burners, or electric, or diesel or hybrid. Thermal cycle at high efficiency. Modular construction for production up to 7.000 kg/h, weight up to 15 Kg/m2. Working width up to 6.5m. Speed up to 150 m\min
The possibility to regulate the volume of air flow for every section separately via frequency inverters, again allows easy production of any kind of web and weight. Within the oven the web is quickly heated in a well balanced way; uniformly melting the bonding fibres and therefore providing optimal homogeneous bonding. The possibility of inversion of the air flow direction in each section separately allows bonding for thick felt, compensating the weight of the fibres also. Web thickness adjusted by the belts distance in various points along the oven length. Various solutions for heat recovering are available.
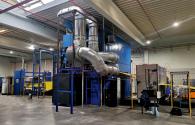
PERFORATED DRUM OVENS
PERFORATED DRUM OVENS
The operating principle in this oven is a combination of a perforated drum with a large centrifugal fan. The fan draws the air out of the drum interior, then it passes through the heating system (normally gas burner) and is forced back to the drum. This generates a vacuum within the drum on which surface the material is held. The material is traversed by a large volume of the hot air which ensures high heat transfer.
Due to the complete penetration of the air throughout the nonwoven product, these ovens are extremely efficient, and require reduced floor space. The drums diameter is optimized accordingly with the speed and the application, and they can vary from 1 to 7,5 meters with speeds up to 800 m\min.
There is also the possibility of adding more than one drum in line to achieve faster speeds.
When the felt is narrower than the width of the drum, two internal adjustable shutters stop the passage of air on the sides of the felt. This is to avoid loss of efficiency due to air flow that does not pass through the felt.
Typical applications: Asiuating needlepunched and impregnat felts, drying lightweight cotton or polyester spunlaced webs, thermfixing needlepunched felts for technical felts.
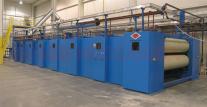
DOUBLE BELT PRESSES
DOUBLE BELT PRESSES
This new machine has been studied and optimized to produce highly dense boards from nonwoven, from any kind of non woven, waste material or particles. The press uses plain and solid belts, that are able to press the product very heavily and cool it while it is still under heavy pressure. The heating of the product is provided by hot plates that transmit the heat to the plain (solid) belts and also hot rolls. The heating time is given by the length of the belt + hot plates, with the heating of the plates and rolls made by forced thermal oil circulation.
These can be warmed up using a gas-fired unit as well as an electric power unit. Cooling of the felt is made by water cooled plates and rolls in contact with the belts, situated in the last part of the module.
Cold water flows into and through the cold plates and rolls, via a centrifugal pump. With the press , which is a combination of calender and oven, the material is ALWAYS under compression.
The belts are supported by the rolls and plates and the pressure is applied for their full length with belt distances adjustable from a central control board.
Applications: Compressing of polyester thermobonded webs, in blend with bico, to produce sound/thermal insulation boards and decorative felts ; Compressing of webs made with cellulose + Bico, used under wooden floors, to prevent noise and to insulate from cement floors; Compressing of needle punched felt made in Kenaf+PP in order to facilitate the 3d forming process in automotive industry ; Compressing of wood-fibers with BIco. This is used to produce medium density wood boards, without the use of an extremely expensive wood production line ; Lamination of two or more felts without any chemicals, just using the fibers; Laminating of shoddy felt with a polyethylene foil, to produce a protective felt for painting; Smoothing of thermobonded product removing marks from the oven belts
Equipping the machine with our powder\particles scattering unit, it is possible to transform any of your waste containing fusible fibers or fusible material into rigid boards that can then be used in various applications.
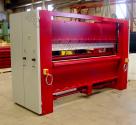
CUTTING MACHINES, END OF LINES
CUTTING MACHINES, END OF LINES
Various cutting solutions according to the characteristics of the products. Guillotine, Disk on fixed carriage, disk in moving carriage (single or double). High speed, thicknesses up to 300mm. Pressure or motorized disc trimming units with automatic sharpening. Special model for wood fibers. Pad stackers at the end of line and or winder optionally.