Bridarolli S.r.l.
Adresse
Bridarolli S.r.l.
Via Fratelli Bandiera 9/L
20835 Muggió Monza-Brianza
Italy
Telefon+39 039 598 6639
Entdecken Sie mehr von uns
Folgen Sie uns auf
Über uns
Armed with a 35 years' experience in the hot melt sector, Bridarolli srl is specialised in engineering and manufacturing hot melt dispensing systems, such as extruders, drum and tank melting units, and coating and lamination equipment, processing different kind of adhesives like PS, UV, TPU, PUR, EVA. Bridarolli srl provides a detailed technical knowledge and a full assistance from the pre-sale to the post-sale, with a 360° technical assistance service composed by skilled technicians.
Our products range includes:
- COATING AND LAMINATION HEADS/APPLICATORS/SLOT DIES;
- MELTERS AND DISPENSERS FOR HOT MELT ADHESIVES (screw extruders - tank units - drum units);
- APPLICATORS/JETTING HEADS - ELECTROPNEUMATIC APPLICATORS;
- HEATED HOSES.
Types of hot melt adhesives to be processed:
- PSA
- EVA
- PUR
- UV
- THERMOPLASTIC
- POLYETHYLINE
- POLYAMIDE
- POLYESTER
- TPU
Main sectors of application:
- COATING & LAMINATION
- TEXTILE - TECHNICAL TEXTILE
- CONVERTING
- ASSEMBLY
- GEOTEXTILE
- MEDICAL
- AUTOMOTIVE
- BUILDING
Unsere Produktgruppen
- Technology and Processes
Unsere Anwendungsbereiche / Lösungen
Keywords
- hotmelt
- lamination
- gluing systems
- melters
- coating
Unsere Produkte
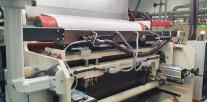
Coating and lamination heads
BH range coating heads are used for the application of adhesives where it is necessary the lamination of two or more materials, such as textiles, for the profile wrapping or to produce films.
Their main purpose can be found in the textile, woodworking, automotive, converting and graphic sector.
BH range coating heads are a highly customizable accessory, as their width can be changed according to the manufacturing requirements of the customer.
These applicators differ for their high reliability, as the adhesive coating will always result uniform and constant.
Strengths of our BH range coating heads are the construction material, as it is a particular steel alloy, and the special hardening treatment applied on the lips: as a matter of fact, we have engineered and developed a specific hardening treatment, in order to obtain a long-lasting and performing final product. This special treatment provides to our heads a high quality of the finish compared to standard treatments, for a uniform coating without stripes and a high endurance against abrasion and productive wear, keeping in this way the product like new and preserving its original technical specifications, guaranteeing a hardness up to 70 HRC.
TYPES OF COATING HEADS:
Flat with lips
Extrusion
With rotating bar
Multimodule
TYPES OF COATING WIDTHS:
Fixed coating width
Adjustable coating width
COATING WIDTH ADJUSTMENT:
Manual handwheels
Automatic motors
TYPES OF ADHESIVES:
Each type with a max. viscosity of 2.000.000 cps
TECHNICAL SPECIFICATIONS:
MODEL COATING WIDTH VISCOSITY OPERATIVE TEMP.
LIP From 30 up to 3.000 mm 2.000 – 100.000 cps Up to 250°C
EXTRUSION From 1.000 up to 4.000 mm 100.000 – 2.000.000 cps Up to 250°C
ROTATING BAR From 300 up to 3.000 mm 2.000 – 200.000 cps Up to 250°C
MULTIMODULE From 300 up to 3.000 mm 2.000 – 50.000 cps Up to 200°C
Applicators/jetting heads
Electropneumatic applicators/jetting heads are used for accurately dispensing the hot melt adhesive already melted and delivered from the heated hose.
They can be manufactured for automatic dispensing, via solenoid valves, or for manual dispensing, via related trigger.
Applicators/jetting heads can be supplied complete with modules, nozzles, solenoid valves etc. and can dispense the hot melt adhesive in beads, dots, lines, spray etc.
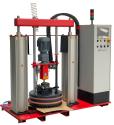
Drum units
BD range drum melting units have been engineered for melting 200 lt or 20 lt barrel adhesives and are the best solution for reactive polyurethane (PUR) adhesives. These kinds of adhesives, in fact, tend to reticulate in contact with oxygen, but thanks to a teflon-coated aluminium plate covering whole drum contents, just the adhesive in contact with the plate will be melted, while the remaining inside the drum will be preserved entirely.
BD range drum melting units can also be used as premelter for the melting of self-adhesives for the following feeding of a tank unit.**
Available on request the tandem working mode for two drum units, in order to avoid the stop of the productive cycle during drum exchange.
All drum melting units are also equipped with remote assistance.
TYPES OF ADHESIVES:
PUR = reactive polyurethane
UV curable
**PSA for the following use in a tank melting system
TYPES OF PLATES:
FLAT
FINNED
HIGH MELT FINNED
- Teflon-coated drip catcher in order to avoid adhesive leaks during drum exchange
- Siemens touch screen operator panel
- MELT ON DEMAND system: the drum unit melts only the adhesive part in contact with the melting plate
TECHNICAL SPECIFICATIONS:
MODEL PLATE MELTING RATE PUMP RATE
BD 200 LM Flat 20 – 30 kg/h From 48 up to 192 kg/h
BD 200 HM Finned 60 – 80 kg/h From 48 up to 192 kg/h
BD 200 HH High melt finned 100 – 120 kg/h From 48 up to 192 kg/h
BD 20 LM Flat 8 – 10 kg/h From 4,8 up to 38,4 kg/h
BD 20 HM Finned 12 – 16 kg/h From 4,8 up to 38,4 kg/h
Tank melting units
BT range tank melting units are used for melting granules or sticks hot melt adhesives.
The structure of the standard melting unit model involves the assembly of a tank plus a grid, guaranteeing a better melting compared to the model assembling just the tank.
Thanks to their structure, BT range tank units result very easy to clean and versatile, due to the different capacities of the adhesive tanks which can be assembled.
BT range tank units are all arranged for installing various communication systems with other machines such as Profinet, Profibus o Modbus.
All tank melting units are also equipped with remote assistance.
TYPES OF ADHESIVES:
UV curable
PSA
EVA
**PUR optional version
TANKS CAPACITIES (lt):
6 – 12 – 25 – 50 - 100 – 160 - 300
- Arrangement for assembling pressure sensors
- Arrangement for assembling loading cells
- Arrangement for assembling tank+grid, in order to guarantee a better melting;
- Available also in the version without grid
- Easy to clean
- Siemens touch screen operator panel
- Profinet / Profibus / Modbus for interfacing with other machines
TECHNICAL SPECIFICATIONS:
MODEL MELTING RATE HEATING ZONES TANK NO. PUMPS
BT 6/1 2 - 4 kg/h 1 6 lt 1
BT 12/1 4 - 8 kg/h 1 12 lt 1
BT 12/2 8 - 10 kg/h 2 12 lt 1 - 2
BT 25/1 8 - 12 kg/h 1 25 lt 1 - 3
BT 25/2 16 - 20 kg/h 2 25 lt 1 - 3
BT 50/1 20 - 30 kg/h 1 50 lt 1 - 3
BT 50/2 40 - 60 kg/h 2 50 lt 1 - 3
BT 100 80 - 100 kg/h 2 100 lt 1 - 3
BT 160 120 - 160 kg/h 2 160 lt 1 - 3
BT 300/2 160 - 200 kg/h 2 300 lt 1 - 4
BT 300/3 200 - 250 kg/h 3 300 lt 1 - 4
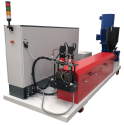
Screw extruders
BE range screw extruders are mainly used for melting hot melt and thermoplastic granules adhesives.
Basically extruders have been engineered in order to face all those adhesives which are difficult to be melted, which require an high operative temperature and are characterized by an high viscosity, compared to all other adhesives normally processed with tank melters.
BE range screw extruders are mainly used with thermoplastics, TPU, polyamides, polyesters and in general with all those adhesives which tend to oxidize.
BE range screw extruders dispose of a particular extrusion screw, designed according to the type of adhesive to be melted.
All extruders are also equipped with remote assistance.
- Special granules feeding system for adhesives requiring a low melting temperature
- Possibility to work in extruder full mouth mode or empty mouth mode
- OPTIONAL: arrangement for degassing system
- Siemens touch screen operator panel
TYPES OF ADHESIVES:
polyester
polyamides
polyethylene
TPU
PU
TECHNICAL SPECIFICATIONS:
MODEL MELTING RATE L/D MOTOR POWER HEATING ZONES
BE 18 6 - 10 kg/h 18/25 2,2 kW 3
BE 30 30 - 40 kg/h 30/30 5,5 kW 3
BE 45 60 - 80 kg/h 45/30 11 kW 3
BE 65 120 - 160 kg/h 65/30 18,5 kW 4
BE 90/25 160 - 200 kg/h 90/25 22,5 kW 4
BE 90/30 300 - 400 kg/h 90/30 30 kW 5
BE 120 500 - 600 kg/h 120/30 75 kW 6
BE 150 600 - 800 kg/h 150/30 110 kW 6
Unsere Ansprechpersonen
Daniele Bridarolli
Engineering/Design
Product Developer
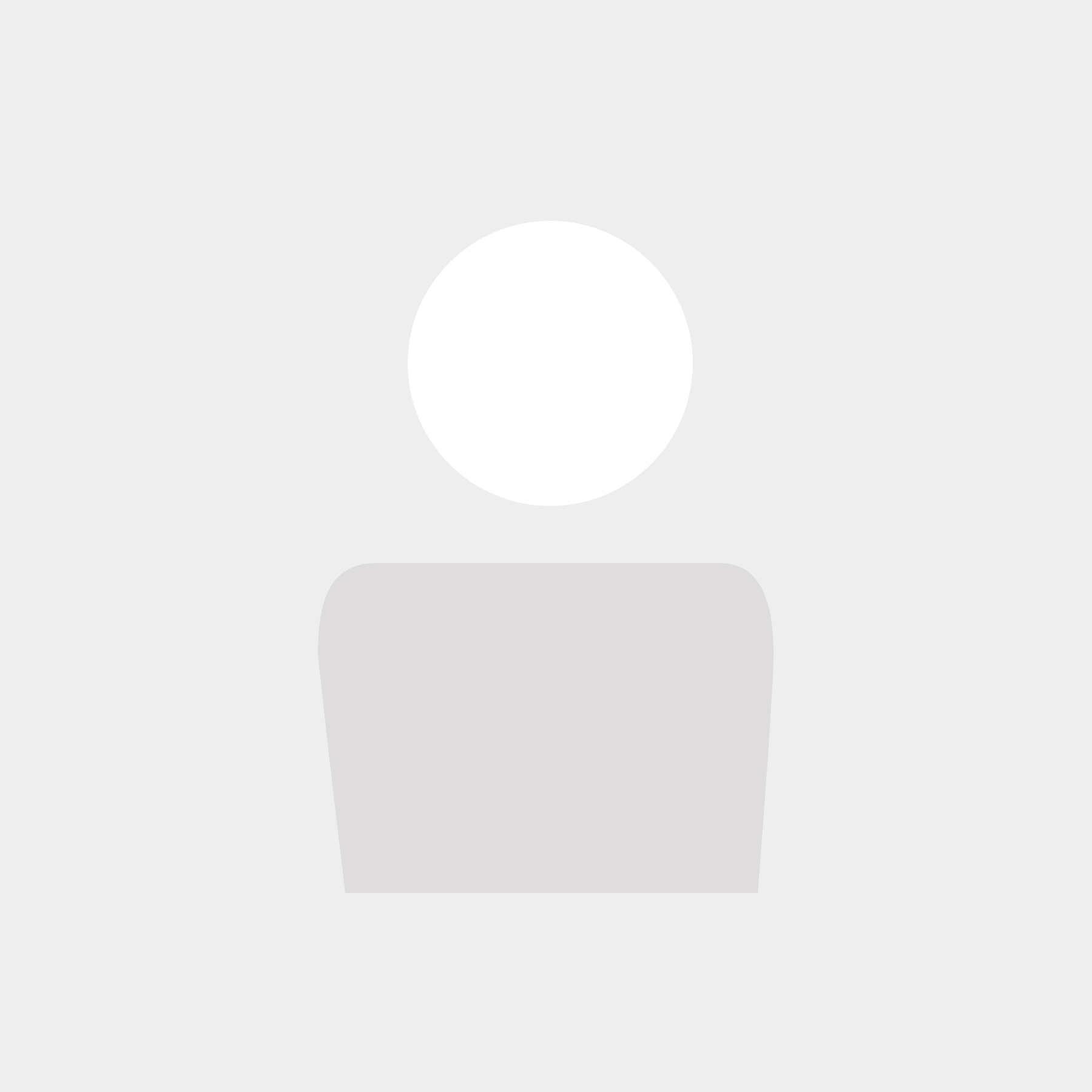