oxytec AG
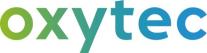
Über uns
Techtextil 2024 - oxytec: Exhaust air treatment process in the textile industry
With exhaust air scrubber and UV/ozone technology to reduce VOCs, formaldehyde, H2S, odour and organic C
oxytec is the market leader in the field of air and water treatment based on photolysis oxidation, low-temperature plasma and scrubbers. We develop and sell systems for the purification and sterilisation of exhaust air, room air, surfaces and waste water in the catering, food, textile and waste disposal industries, in solvent-based processes, in the medical sector and for many other purposes worldwide.
In the textile industry, coating processes are used in the manufacture of technical textiles to provide fabrics or yarns with specific properties such as hydrophobicity. The coating agents can consist of organic products that are applied in aqueous or solvent-based form. This is followed by thermal treatment, during which all volatile components of the coating are released into the exhaust air (VOC, formaldehyde). In addition, the exhaust air also contains some of the fuels used in directly heated stenter frames, such as methane.
This exhaust air can be effectively treated with UV/ozone technology.
The environmentally friendly UV/ozone air purification process is based on the principle of photolysis oxidation. The exhaust air flows through special UV light-producing tubes (photozone lamps). Their radiation breaks down the organic molecular chains and converts natural oxygen (O2) into reactive oxygen (O3).Organic and odorous substances are oxidised. Photocatalytic degradation processes on the surface of the downstream catalyst effectively destroy the remaining odorous substances.All residues are completely biodegradable and are removed with the exhaust air flow. oxytec guarantees an odour reduction of 95 percent and an organic C and formaldehyde content in accordance with TA Luft.
Structure of the Clean Exhaust Air (CEA) systems
A CEA system always consists of the following components:Irradiation chamber with UV lamps (UV/ozone tubes)
Automatic CIP system
Control system
Reaction section up to the fan or downstream unit (e.g. catalyser)
A high penetration depth of the UV light must be achieved for optimum utilisation of the UV radiation output. This is achieved in an irradiation chamber with cross flow. The cross-section of the radiation chamber is determined by the exhaust air volume. The number of UV lamps depends on the air volume and the load of the exhaust air. The CIP cleaning system automatically keeps the UV lamps free of any deposits. It is operated automatically via the control system.
Further system components round off the photolysis oxidation/photooxidation process
To achieve even better results, the UV-C/ozone technology can be supplemented with additional system components:
Scrubber (W)
The oxytec exhaust air scrubbers effectively destroy water-soluble and odour-carrying particles in the exhaust air.The combination with a scrubber has proven to be particularly effective for exhaust air from laboratories, animal stables and smokehouses.It removes soluble components such as ammonia, reduces the exhaust air temperature before photolysis oxidation and enriches the exhaust air flow with moisture. In the textile industry, it cools the air and separates particles.Reaction section (R) after the UV/ozone chamberThe reaction section is dimensioned so that the substances to be degraded are oxidised for 3 seconds before they are released into the outside air via the fan or catalytic converter.
Catalyst (KAT) after the UV/ozone chamber
The activated carbon serves as a reaction surface for very long-chain molecules and for excess ozone in the event of load fluctuations. In wastewater treatment plants, the catalyser is used to separate the sulphur produced.
The advantages at a glance:
Compliance with official requirements (TA Luft, organic C, formaldehyde, odour requirements)
Low energy consumption (significantly lower investment costs compared to thermal post-combustion processes, significantly reduced maintenance and operating costs, on/off system)
Easy to retrofit (low construction costs, small space requirement, roof installation possible, simple installation)
Environmentally friendly (no use of chemicals, no waste water pollution, low CO2, all residues are 100% biodegradable)
Unsere Produktgruppen
- Technology and Processes
Unsere Anwendungsbereiche / Lösungen
Keywords
- Abluftreinigung/Exhaust air cleaning
- Energierückgewinnung/Energy recovery
- Spannrahmenabluft/Tensioning frame exhaust air
- Formaldehydreduzierung/Formaldehyde reduction
Unsere Produkte
CWA
This exhaust air scrubber effectively removes water-soluble and odour-bearing particles in the exhaust air. This has proved particularly effective for ammonium-contaminated exhaust air from laboratories, animal stables, slaughterhouses and animal processing plants. Pollutants are effectively separated from the exhaust air.
Function
The scrubbing liquid sprays against the air flow, thus achieving the highest degree of scrubbing for toxic gases and odorous substances.
The washed-out substances are concentrated and separated by a sump.
More than 99 % of chlorine gas, ammonia and hydrochloric acid vapours are removed.
Reduction of the exhaust air temperature
Enriches the exhaust air stream with moisture
Use
Often used in the textile industry as a pre-cleaning stage upstream of the CEA system, to reduce the exhaust air temperature.
Laboratories, coating processes
Optimised for fluctuating raw gas loads
Animal houses, slaughterhouses and animal processing plantsTechnology & material
- Scrubber counterflow principle
- Stainless steel 4301
Installation & maintenance
- Easy
- Very low maintenance
Additional information
- Low pressure drop
- Dosing of chemicals according to demand
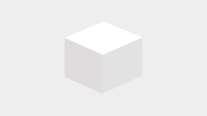
AAH 3000 Air Air Heatrecovery
This air-to-air heat recovery unit is designed for integration into an exhaust air system with a high dirt load, e.g. dust, aerosols from industrial exhaust air after drying processes. To cool the process exhaust air, the cold fresh air is passed through segments in a counterflow process.
Function
- During operation, this segment design provides a large heat transfer surface for optimum utilisation for heat transfer from the hot extract air to the cold fresh air.
- Clean fresh air flows through the segments
- No radiation losses, as the heated fresh air is returned directly to the system with optimised heat transfer (segment design).
Use
- No change to the existing process lines
- Economical to use from 1300 m³/h upwards
Technology & material
- Stainless steel design
- Low pressure drop
Installation & maintenance
- Modular construction, fully assembled and ready for direct installation
- Low space requirement
- The unit is integrated into the existing exhaust air duct without changing the exhaust air duct.
- Minimal cleaning effort
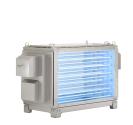
CEA 48
This exhaust air unit is designed for exhaust air purification in industry. The air purification process of this unit takes place in three steps and thus effectively reduces VOCs/total C, formaldehyde, H²S, odours and fats in the industrial exhaust air.
The system complies with all official requirements according to TA Luft (total C, formaldehyde, aromatics, mercaptans, odour limits).
Function
Breakdown of long-chain compounds by UV light (photolysis) into radical compounds
Formation of ozone and hydroxyl radicals and their decay products
Reaction of the ozone with the split compounds (oxidation) in the subsequent reaction section
Cross-flowing of the exhaust air in the irradiation chamber achieves a high penetration depth of the UV light, and thus optimum utilisation of the radiation power